Halogen-free flame-retardant ABS (Acrylonitrile Butadiene Styrene) resin and preparation method thereof
A technology of ABS resin and ammonium polyphosphate, applied in the field of flame retardant, can solve the problems of strong hygroscopicity, inconvenient processing, poor compatibility, etc.
- Summary
- Abstract
- Description
- Claims
- Application Information
AI Technical Summary
Problems solved by technology
Method used
Image
Examples
Embodiment 1
[0023] 1) Dry 700g of ABS resin, 225g of ammonium polyphosphate and montmorillonite nanocomposite, and 75g of dipentaerythritol in a forced air drying oven at 80°C for 3 hours;
[0024] 2) Mix the ABS resin obtained in step 1), ammonium polyphosphate and montmorillonite nanocomposite, dipentaerythritol, 3g of polytetrafluoroethylene, 4g of 168 antioxidant and 2g of 1010 antioxidant;
[0025] 3) The mixture obtained in step 2) is melt-blended with a twin-screw extruder, extruded and granulated. The temperature settings of the extruder from the feed port to the head are 186°C, 191°C, 196°C, 196°C, 191°C, 185°C.
[0026] 4) Dry the granulated particles in step 3) in an oven at 80°C for 2 hours, then inject them on the injection molding machine, and inject splines of the following sizes: 120mm×6mm×3mm, 127mm×12.7mm×3.2mm, 127mm ×12.7mm×1.6mm, and 100mm×100mm×3mm; the temperature of each section of the injection molding machine is set to 205°C, 205°C, 205°C, 200°C, 195°C, and the ...
Embodiment 2
[0029] Same as Example 1, except that the mass of ABS resin in step 1) is 600g, the mass of ammonium polyphosphate and montmorillonite nanocomposite is 300g, and the mass of dipentaerythritol is 100g. The test results are shown in Table 1.
Embodiment 3
[0031] 1) Bake 700g of ABS resin, 225g of ammonium polyphosphate and montmorillonite nanocomposite, 75g of dipentaerythritol and 30g of coated red phosphorus in a blast drying oven at 80°C for 3h;
[0032] 2) Combine the ABS resin obtained in step 1), ammonium polyphosphate and montmorillonite nanocomposite, dipentaerythritol, coated red phosphorus with 3g of polytetrafluoroethylene, 4g of 168 antioxidant and 2g of 1010 antioxidant well mixed;
[0033] 3) The mixture obtained in step 2) is melt-blended with a twin-screw extruder, extruded and granulated. The temperature settings of the extruder from the feed port to the head are 186°C, 191°C, 196°C, 196°C, 191°C, 185°C.
[0034] 4) Dry the granulated particles in step 3) in an oven at 80°C for 2 hours, then inject them on the injection molding machine, and inject splines of the following sizes: 120mm×6mm×3mm, 127mm×12.7mm×3.2mm, 127mm ×12.7mm×1.6mm, and 100mm×100mm×3mm; the temperature of each section of the injection moldin...
PUM
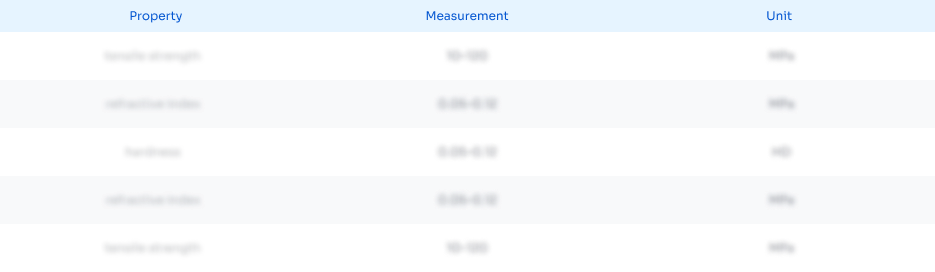
Abstract
Description
Claims
Application Information

- R&D Engineer
- R&D Manager
- IP Professional
- Industry Leading Data Capabilities
- Powerful AI technology
- Patent DNA Extraction
Browse by: Latest US Patents, China's latest patents, Technical Efficacy Thesaurus, Application Domain, Technology Topic, Popular Technical Reports.
© 2024 PatSnap. All rights reserved.Legal|Privacy policy|Modern Slavery Act Transparency Statement|Sitemap|About US| Contact US: help@patsnap.com