Multi-product cleaning and producing method with coal gangue comprehensive utilization
A technology of clean production and coal gangue, applied in steam generation methods, combustion methods, cement production, etc., can solve problems such as wall cracking, high drying shrinkage, and failure to meet wall insulation requirements, so as to avoid secondary volatilization, The effect of achieving zero emissions
- Summary
- Abstract
- Description
- Claims
- Application Information
AI Technical Summary
Problems solved by technology
Method used
Image
Examples
Embodiment 1
[0059] Embodiment 1: Raw material: adopt the raw meal that certain factory prepares. Its raw material rate value is:
[0060] Lime saturation coefficient KH=0.872, silica ratio SM=2.41, alumina ratio AM=1.76
[0061] See Table 1 for the calorific value, ratio and coal consumption of the blended fuel.
[0062] Table 1: Fuel Consumption
[0063]
[0064] The heat consumption of cement firing in Example 1 is based on the existing lower heat consumption value, the thermal model does not include clinker firing, and the actual firing heat supply is based on the temperature of the flue gas entering the kiln series calciner; the mixed fuel The calorific value brought in is brought in by the flue gas, and the composition of unburned matter in the flue gas is based on the CO content of the flue gas entering the furnace.
[0065] The experimental results are:
[0066] The flue gas temperature of the calciner entering the kiln series is 1050°C, and the flue gas temperature of the w...
Embodiment 2
[0069] Example 2: The experimental source and fuel conditions are the same as in Example 1, only the CO content of the flue gas entering the furnace is controlled, and the proportion of unburned substances carried by the flue gas is appropriately increased.
[0070] The experimental results are:
[0071] The flue gas temperature of the calciner entering the kiln series is 1045°C, and the flue gas temperature of the waste heat boiler entering the kiln series is 921°C.
[0072] The flue gas temperature of the calciner entering the furnace series is 911°C, the CO content of the flue gas entering the furnace is 6.37%, the flue gas temperature of the waste heat boiler entering the furnace series is 583°C, and the raw material decomposition rate of the exiting device is 95.5%.
[0073] The two sets of waste heat boilers can generate 393.8 KW.h / t. clinker, the circulating fluidized bed boiler can generate 336.7 KW.h / t. clinker, and the total power generation is 630.5 KW.h / t. clinker ...
Embodiment 3
[0074] Embodiment 3: The raw material conditions are the same. In this experiment, the high-quality coal consumption of cement firing was reduced, so that the heat consumption of cement firing was lower than the existing firing heat consumption value, and the proportion of mixed fuel was increased at the same time.
[0075] See Table 2 for the calorific value, ratio and coal consumption of the blended fuel.
[0076] Table 2 Fuel consumption
[0077]
[0078] The experimental results are:
[0079] The flue gas temperature of the calciner entering the kiln series is 1045°C, and the flue gas temperature of the waste heat boiler entering the kiln series is 779°C.
[0080] The flue gas temperature of the calciner entering the furnace series is 795°C, the CO content of the flue gas entering the furnace is 5.22%, the flue gas temperature of the waste heat boiler entering the furnace series is 609°C, and the raw material decomposition rate of the exiting device is 91.3%.
[0081...
PUM
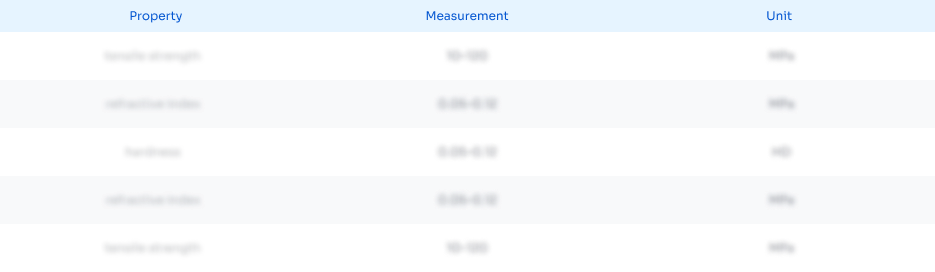
Abstract
Description
Claims
Application Information

- R&D
- Intellectual Property
- Life Sciences
- Materials
- Tech Scout
- Unparalleled Data Quality
- Higher Quality Content
- 60% Fewer Hallucinations
Browse by: Latest US Patents, China's latest patents, Technical Efficacy Thesaurus, Application Domain, Technology Topic, Popular Technical Reports.
© 2025 PatSnap. All rights reserved.Legal|Privacy policy|Modern Slavery Act Transparency Statement|Sitemap|About US| Contact US: help@patsnap.com