Preparation method of self-preheating laser engineered net shaped ZrO2-Al2O3 composite ceramic thin-walled part
A zro2-al2o3, laser forming technology, applied in the field of laser forming, can solve the problems of slow heating process, complicated heating device and high cost, and achieve the effect of dense ceramic structure, few preparation processes and short manufacturing cycle
- Summary
- Abstract
- Description
- Claims
- Application Information
AI Technical Summary
Problems solved by technology
Method used
Image
Examples
Embodiment 1
[0038] As shown, the self-preheated laser shaped ZrO 2 -Al 2 o 3 Composite ceramic thin-walled method, the embodiments of the present invention require: ZrO 2 -Al 2 o 3 The composite ceramic thin-walled parts are 16 mm in length, 2.5 mm in width and 6 mm in height, and the ZrO 2 -Al 2 o 3 The composite powder is laser formed, and the specific forming steps are as follows:
[0039] A. Select 42 ~ 90 μm spherical ZrO as required 2 (including 8wt.%Y 2 o 3 ) powder and Al 2 o 3 (Containing 13wt.%TiO 2 ), put the powder into an electric blast drying oven and dry at 100 °C for 4 hours;
[0040] B. Before processing, the substrate 6 is polished with sandpaper and cleaned with alcohol;
[0041] C. Put the dried powder into the two cylinders of the powder feeder 7 respectively, and adjust the working distance between the bottom end of the nozzle 3 and the surface of the substrate 6 to 9 mm;
[0042] D. Adjust the laser processing parameters: the laser power is 236 W, the...
Embodiment 2
[0046] As shown, the self-preheated laser shaped ZrO 2 -Al 2 o 3 Composite ceramic thin-walled method, the embodiments of the present invention require: ZrO 2 -Al 2 o 3 The composite ceramic thin-walled parts are 16 mm in length, 2.3 mm in width and 6 mm in height, and the ZrO 2 -Al 2 o 3 The composite powder is laser formed, and the specific forming steps are as follows:
[0047] A. Select 42 ~ 90 μm spherical ZrO as required 2 (including 8wt.%Y 2 o 3 ) powder and Al 2 o 3 (Containing 13wt.%TiO 2 ), put the powder into an electric blast drying oven and dry at 100 °C for 4 hours;
[0048] B. Before processing, the substrate 6 is polished with sandpaper and cleaned with alcohol;
[0049] C. Put the dried powder into the two cylinders of the powder feeder 7 respectively, and adjust the working distance between the bottom end of the nozzle 3 and the surface of the substrate 6 to 9 mm;
[0050] D. Adjust the laser processing parameters: the laser power is 200 W, the...
PUM
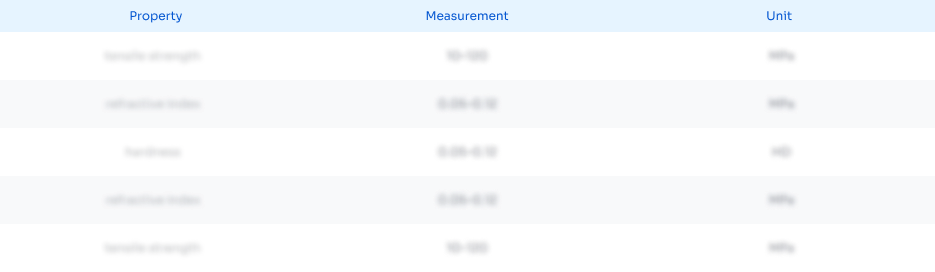
Abstract
Description
Claims
Application Information

- R&D
- Intellectual Property
- Life Sciences
- Materials
- Tech Scout
- Unparalleled Data Quality
- Higher Quality Content
- 60% Fewer Hallucinations
Browse by: Latest US Patents, China's latest patents, Technical Efficacy Thesaurus, Application Domain, Technology Topic, Popular Technical Reports.
© 2025 PatSnap. All rights reserved.Legal|Privacy policy|Modern Slavery Act Transparency Statement|Sitemap|About US| Contact US: help@patsnap.com