Flux used for recycling magnesium alloy cuttings, and preparation method and application method thereof
An application method and technology of magnesium alloy, applied in the field of magnesium alloy metallurgy, can solve the problems of low recovery rate of magnesium scraps, poor effect, lack of safety and economy, etc., to improve recovery safety, prevent oxidative combustion, combustion and other problems. The effect of reducing the risk of explosion
- Summary
- Abstract
- Description
- Claims
- Application Information
AI Technical Summary
Problems solved by technology
Method used
Examples
Embodiment 1
[0011] The main composition and mass fraction of the flux are: 10% anhydrous carnallite, 40% magnesium chloride, 40% potassium chloride, 3% magnesium carbonate, and 7% calcium chloride. Mix the above-mentioned ingredients in the form of powder according to the stated ratio, so that several ingredients are completely mixed together to obtain a flux.
[0012] The application method is as follows: mix 2Kg of flux with 200Kg of magnesium-manganese alloy sacrificial anode chips evenly, and then put 1.5 tons into a furnace heated to 985-1020K to heat up with the furnace. After the chips are melted, add raw magnesium ingots to the furnace capacity, and refine according to the normal process And alloying, and then semi-continuous casting of magnesium-manganese alloy ingots. The prepared magnesium-manganese alloy ingot is hot-extruded by a normal process to make a magnesium-manganese alloy sacrificial anode. After weighing and measuring, the recovery rate of magnesium shavings was cal...
Embodiment 2
[0016] The main components and mass fractions of the flux are: 80% anhydrous carnallite, 5% potassium chloride, 0.5% magnesium carbonate, 2% calcium carbonate, 10% sodium chloride, and 2.5% calcium chloride. Grind the above-mentioned ingredients according to the stated ratio and stir them thoroughly, so that several ingredients are completely mixed together to obtain a flux.
[0017] The application method is as follows: mix 1.5Kg of flux with 200Kg of AZ91D magnesium alloy chips evenly, and then put it into a furnace with a capacity of 1.5 tons heated to 973-993K. After the chips are melted, add magnesium ingot raw materials to the capacity of the furnace, and refine according to the normal process And alloying, and then cast into magnesium alloy parts. The recovery rate of magnesium shavings is measured to reach 93%, and the mechanical properties of the obtained parts meet the requirements of the AZ91D magnesium alloy standard, as shown in Table 2.
[0018] Table 2 Properti...
Embodiment 3
[0021] The flux composition and its mass fraction are: 50% anhydrous carnallite, 3% calcium chloride, 10% magnesium chloride, 20% potassium chloride, 1.5% magnesium carbonate, 0.5% calcium carbonate, and 15% sodium chloride. Mix the above-mentioned ingredients in the form of powder according to the stated ratio, so that several ingredients are completely mixed together to obtain a flux.
[0022] The application method is as follows: mix 6Kg of flux with 200Kg of magnesium-manganese alloy sacrificial anode chips, and then put 1.5 tons into a furnace heated to 773-873K to heat up with the furnace. After the chips are melted, add magnesium ingot raw materials to the capacity of the furnace for refining and alloying. Magnesium-manganese alloy ingots are produced by chemical and other follow-up processes.
PUM
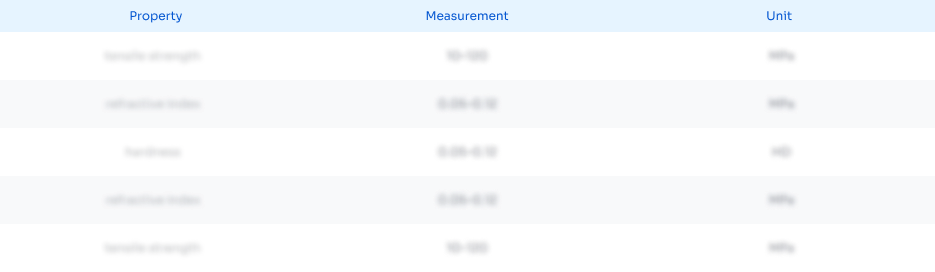
Abstract
Description
Claims
Application Information

- R&D Engineer
- R&D Manager
- IP Professional
- Industry Leading Data Capabilities
- Powerful AI technology
- Patent DNA Extraction
Browse by: Latest US Patents, China's latest patents, Technical Efficacy Thesaurus, Application Domain, Technology Topic, Popular Technical Reports.
© 2024 PatSnap. All rights reserved.Legal|Privacy policy|Modern Slavery Act Transparency Statement|Sitemap|About US| Contact US: help@patsnap.com