Production method for vanadium nitride ferroalloy
A ferro-vanadium nitride alloy and production method technology, applied in metal material coating technology, solid-state diffusion coating, coating, etc., can solve the problems of affecting the effective diffusion of nitrogen, low production efficiency, long production cycle, etc., and achieve product quality The effects of stability, high production efficiency, and high labor productivity
- Summary
- Abstract
- Description
- Claims
- Application Information
AI Technical Summary
Problems solved by technology
Method used
Image
Examples
Embodiment 1
[0023] Mix 5,000 grams of vanadium-iron alloy powder containing 54.2% vanadium into a ball mill, pass through a 80-mesh screen, put the powdered material after mixing into a graphite tank coated with lime powder, and place the graphite tank in the pusher kiln. In the feeding bin, the material is controlled by PLC, automatically enters and exits the pusher kiln, and is heated by electrodes on the outside of the pusher kiln, and the inside is 220m 3 Nitrogen per hour, the pressure in the kiln is kept at 0.6-0.7MPa, and the high-temperature nitriding and sintering reactions are carried out. After the powdery material enters the kiln for 28 hours, it is automatically released from the furnace and cooled under the protection of nitrogen to obtain ferrovanadium nitride. The composition is: V : 43.78%, N: 9.03%, C: 1.34%, Si: 0.99%, P: 0.071%, Al: 1.35%, Mn: 0.29%.
Embodiment 2
[0025] Mix 4800 grams of vanadium-containing 80.2% powder, 400 grams of vanadium oxide, and 350 grams of graphite powder into a ball mill, pass through a 120-mesh sieve, and put the powdered material after mixing into a graphite tank coated with lime powder. Put the graphite material tank in the feeding bin of the tunnel kiln, so that the material is controlled by PLC, automatically enters and exits the tunnel kiln, is heated outside the tunnel kiln, and passes through 240m inside 3 Nitrogen per hour, the pressure in the kiln is maintained at 0.7-0.8MPa, and the carbon heat, nitriding and sintering reactions are carried out. After the powdery material enters the kiln for 16 hours, it is automatically released from the furnace and cooled under the protection of nitrogen to obtain ferrovanadium nitride. Its composition is : V: 70.83%, N: 13.59%, C: 1.46%, Si: 1.75%, P: 0.051%, Al: 1.60%, Mn: 0.42%.
Embodiment 3
[0027] Mix 3,860 grams of vanadium oxide containing 63.5% vanadium, 550 grams of graphite powder, and 1,700 grams of iron powder into a ball mill, pass through a 100-mesh sieve, and put the mixed powder into a ceramic material tank coated with lime powder , put the ceramic material tank in the feeding bin of the pusher kiln, so that the material is controlled by PLC, automatically enters and exits the pusher kiln, is heated outside the pusher kiln, and the inside is 230m 3 Nitrogen per hour, the pressure in the kiln is maintained at 0.4-0.5MPa, and the carbon heat, nitriding and sintering reactions are carried out. After the powdery material enters the kiln for 16 hours, it is automatically released from the furnace and cooled under the protection of nitrogen to obtain ferrovanadium nitride. Its composition is : V: 49.28%, N: 10.46%, C: 1.78%, Si: 1.02%, P: 0.049%, Al: 0.60%, Mn: 0.36%.
PUM
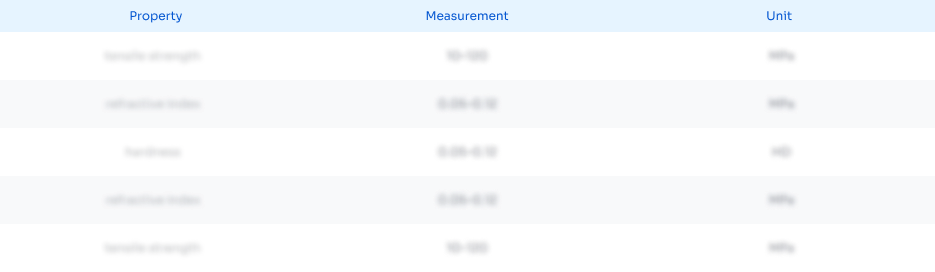
Abstract
Description
Claims
Application Information

- R&D
- Intellectual Property
- Life Sciences
- Materials
- Tech Scout
- Unparalleled Data Quality
- Higher Quality Content
- 60% Fewer Hallucinations
Browse by: Latest US Patents, China's latest patents, Technical Efficacy Thesaurus, Application Domain, Technology Topic, Popular Technical Reports.
© 2025 PatSnap. All rights reserved.Legal|Privacy policy|Modern Slavery Act Transparency Statement|Sitemap|About US| Contact US: help@patsnap.com