Light emitting diode (LED) encapsulation adhesive composition
A technology of LED packaging and composition, applied in the direction of adhesives, adhesive additives, non-polymer adhesive additives, etc., can solve the problems of decreased strength, poor light transmittance, yellowing, etc.
- Summary
- Abstract
- Description
- Claims
- Application Information
AI Technical Summary
Problems solved by technology
Method used
Image
Examples
preparation example Construction
[0023] One, the preparation of polysiloxane A
[0024] The general structural formula that the present invention relates to polysiloxane A is:
[0025]
[0026] where R 1 Is an alkyl group, such as methyl, ethyl, propyl, butyl, etc., preferably methyl; R 2 Is alkyl or alkenyl, such as methyl, vinyl, allyl, butenyl, etc., preferably vinyl; R 3 Aryl, such as phenyl, tolyl, naphthyl, etc., preferably phenyl. a+b+c+d+e=100, a=1~20, b=0~20, c=0~20, d=0~20, e=30~60.
[0027] The preparation method of the present invention relates to polysiloxane A: add catalyst, solvent, end-capping agent, methyl siloxane, methyl vinyl siloxane, phenyl siloxane dropwise while stirring at room temperature or under heating Phenyltrialkoxysilane, after dripping phenyltrialkoxysilane, react at room temperature or under heating for 3~18 hours, stand still, separate the upper layer of acid water, add water to the lower oil phase, wash the oil phase into the middle properties, and then at 150 ° C,...
Embodiment 1
[0034] Put 20g of 30% sulfuric acid, 54g of toluene, 40g of hexamethyldisiloxane, 22g of octamethylcyclotetrasiloxane and 26g of tetramethyltetravinylcyclotetrasiloxane into a four-necked bottle, start stirring, Slowly add phenyltrimethoxysilane dropwise, after dripping 178g of phenyltrimethoxysilane, react at room temperature for 18 hours, stand still, separate the upper layer of acid water, add water to the lower oil phase, and wash the oil phase to neutral , and then at 150 ° C, -0.099Mpa to pull out the low fraction to obtain a colorless and transparent product A1.
Embodiment 2
[0036] Put 25g of 30% sulfuric acid, 107g of toluene, 30g of hexamethyldisiloxane, 88g of dimethyldimethoxysilane and 49g of tetramethyltetravinylcyclotetrasiloxane into a four-necked bottle, and put it under reflux Turn on the stirring tube, start to slowly add phenyltrimethoxysilane dropwise, after dripping 400g of phenyltrimethoxysilane, stir at room temperature for 16 hours, stand still, remove the upper layer of acid water, and wash the lower layer of oil phase with water , wash the oil phase to neutrality, and then pull out the low fraction at 150°C and -0.099Mpa to obtain a colorless and transparent product A2.
PUM
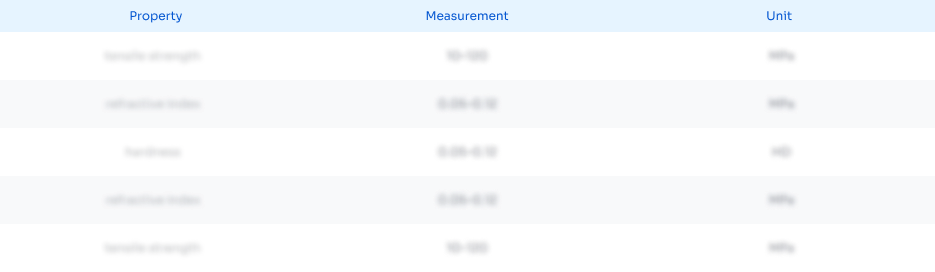
Abstract
Description
Claims
Application Information

- Generate Ideas
- Intellectual Property
- Life Sciences
- Materials
- Tech Scout
- Unparalleled Data Quality
- Higher Quality Content
- 60% Fewer Hallucinations
Browse by: Latest US Patents, China's latest patents, Technical Efficacy Thesaurus, Application Domain, Technology Topic, Popular Technical Reports.
© 2025 PatSnap. All rights reserved.Legal|Privacy policy|Modern Slavery Act Transparency Statement|Sitemap|About US| Contact US: help@patsnap.com