High-performance calcium sulfonate complex grease and preparation method thereof
A technology of composite calcium sulfonate and high-basic calcium sulfonate, applied in the chemical field, can solve the problems of low thickening ability of calcium sulfonate solution, low sintering load of lubricating grease, poor high temperature performance, etc., and solve the problem of surface hardening , long service life, complete conversion effect
- Summary
- Abstract
- Description
- Claims
- Application Information
AI Technical Summary
Problems solved by technology
Method used
Image
Examples
Embodiment 1
[0037] In this embodiment, the raw materials are prepared in the following steps to prepare composite calcium sulfonate base grease:
[0038] Step 1. Mix 32.08% of 150BS base oil, 38.25% of 380TBN calcium petroleum sulfonate and 10.5% calcium carbonate in an open reactor with a steam jacket and double-moving paddles, and heat to 75°C;
[0039] Step 2. Add 2.58% isopropanol, 3.52% water and 1.25% cetylbenzenesulfonic acid to the above mixture, heat to 102°C, and keep stirring at this temperature for 45min until form a gel;
[0040] Step 3. When forming a gel, add 2.5% calcium hydroxide and heat up to 115°C, then add 1.85% 12-hydroxystearic acid at a rate of 4kg / min, stir for 15min, and then add 12-hydroxystearic acid at a rate of 3kg / min Add 2.15% sulfuric acid, continue to stir and react for 30min;
[0041]Step 4. Raise the temperature of the reaction system to 126°C, add 3.12% polyisobutene, continue to raise the temperature of the reactant system to 175°C, and refine a...
Embodiment 2
[0045] In this embodiment, the raw materials are prepared in the following steps to prepare composite calcium sulfonate base grease:
[0046] Step 1. Mix 30.71% intermediate base oil, 41.44% 400TBN synthetic calcium sulfonate and 7.89% calcium carbonate in an open reactor with steam jacket and double-moving blades, and heat to 66°C;
[0047] Step 2: Add 3.16% isopropanol, 4.74% water and 1.3% dodecylbenzenesulfonic acid to the above mixture, heat to 107°C, and keep stirring at this temperature for 60min until form a gel;
[0048] Step 3. When forming a gel, add 2.29% calcium hydroxide, and raise the temperature to 116°C, add 0.31% glacial acetic acid to the reaction system, and react for 20 minutes, then add 2.96% 12-hydroxyl at 6kg / min Stearic acid, after stirring and reacting for 20min, add 1.97% phosphoric acid at a speed of 2kg / min, continue stirring and reacting for 20min;
[0049] Step 4. Raise the temperature of the reaction system to 130°C, add 1.26% polystyrene-isob...
Embodiment 3
[0053] In this embodiment, the raw materials are prepared in the following steps to prepare composite calcium sulfonate base grease:
[0054] Step 1. Mix 31.46% polyalphaolefin, 32.86% 400TBN synthetic calcium sulfonate and 12.28% calcium carbonate in an open reactor with a steam jacket and double-moving paddles, and heat to 85°C;
[0055] Step 2. Add 3.43% isopropanol, 5.21% water and 1.42% octadecylbenzenesulfonic acid to the above mixture, heat to 110°C, and keep stirring at this temperature for 90min until form a gel;
[0056] Step 3. When forming a gel, add 1.98% calcium hydroxide, and raise the temperature to 120°C, add 0.18% glacial acetic acid to the reaction system, and react for 25 minutes, then add 3.32% 12 at a speed of 8kg / min -Hydroxystearic acid, after stirring and reacting for 20min, add 2.13% nitric acid at a speed of 5kg / min, continue stirring and reacting for 30min;
[0057] Step 4. Raise the temperature of the reaction system to 145°C, add 2.48% polymethy...
PUM
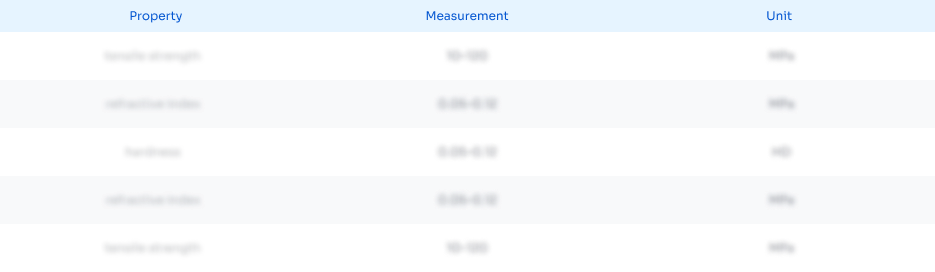
Abstract
Description
Claims
Application Information

- Generate Ideas
- Intellectual Property
- Life Sciences
- Materials
- Tech Scout
- Unparalleled Data Quality
- Higher Quality Content
- 60% Fewer Hallucinations
Browse by: Latest US Patents, China's latest patents, Technical Efficacy Thesaurus, Application Domain, Technology Topic, Popular Technical Reports.
© 2025 PatSnap. All rights reserved.Legal|Privacy policy|Modern Slavery Act Transparency Statement|Sitemap|About US| Contact US: help@patsnap.com