Three-stream spiral wound type heat exchange equipment for secondary refrigeration and low-temperature liquefaction of LNG (liquefied natural gas)
A secondary refrigeration, spiral winding technology, applied in the direction of liquefaction, indirect heat exchanger, heat exchanger type, etc., can solve the problems of complex heat exchange process, scrapped heat exchanger, small temperature difference, etc.
- Summary
- Abstract
- Description
- Claims
- Application Information
AI Technical Summary
Problems solved by technology
Method used
Image
Examples
Embodiment Construction
[0014] Connect the natural gas pipeline with a primary outlet temperature of -53°C to the natural gas inlet connection pipe 29, and the natural gas enters the natural gas inlet pipe box 30 at -53°C and 5.8 MPa, and then distributes it to the branch pipes of the natural gas spiral tube bundle 32 in the pipe box 30. After the tube bundle 32 is helically wound, it is in the cylinder 12 and the throttled C 2 h 4 , N from Level 3 and into Takeover 2 2 —CH 4 The mixed refrigerant performs heat exchange, and liquefies when the temperature drops to -120° C. and the pressure drops to 5.5 MPa. After liquefaction, it flows to the pipe box 39 and flows into the third-stage refrigeration device through the connecting pipe 40 for supercooling.
[0015] N 2 —CH 4 The mixed refrigerant enters the mixed refrigerant pre-cooling tube box 17 at -53°C and 1.88 MPa, and then distributes in the tube box 17 to each branch of the tube bundle 15. The tube bundle 15 is throttled in the cylinder 12 a...
PUM
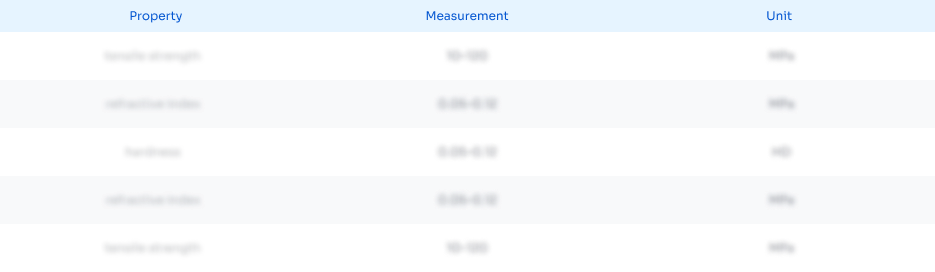
Abstract
Description
Claims
Application Information

- R&D
- Intellectual Property
- Life Sciences
- Materials
- Tech Scout
- Unparalleled Data Quality
- Higher Quality Content
- 60% Fewer Hallucinations
Browse by: Latest US Patents, China's latest patents, Technical Efficacy Thesaurus, Application Domain, Technology Topic, Popular Technical Reports.
© 2025 PatSnap. All rights reserved.Legal|Privacy policy|Modern Slavery Act Transparency Statement|Sitemap|About US| Contact US: help@patsnap.com