Extruder screw
A technology of extruder and screw, which is applied in the field of machinery for processing solid resin materials, and can solve problems such as unguaranteed spinning quality and difficulty in melting in the metering section.
- Summary
- Abstract
- Description
- Claims
- Application Information
AI Technical Summary
Problems solved by technology
Method used
Image
Examples
Embodiment Construction
[0015] The extruder screw provided by the embodiment of the present invention is used for melt spinning of high-density polyethylene, based on its melt index of 4, spinning temperature of 200°C to 250°C, and density of 0.94kg / m 3 to 0.96kg / m 3 , as well as the rheology, heat capacity and other properties of the material, a screw suitable for melt spinning polyethylene monofilament is designed.
[0016] see figure 1 and figure 2 , the extruder screw provided by the embodiment of the present invention, the main body of the screw structure includes a feed section 1 , a compression section 2 , a mixing section 3 and a metering section 4 . The feed section 1 is a constant root diameter; the compression section 2 is a gradual increase in the root diameter, and the screw channel gradually becomes shallow; the metering section 4 is a constant root diameter; the 3 root diameters of the mixing section vary with the At the same time, the mixing section 3 is moved from the conventiona...
PUM
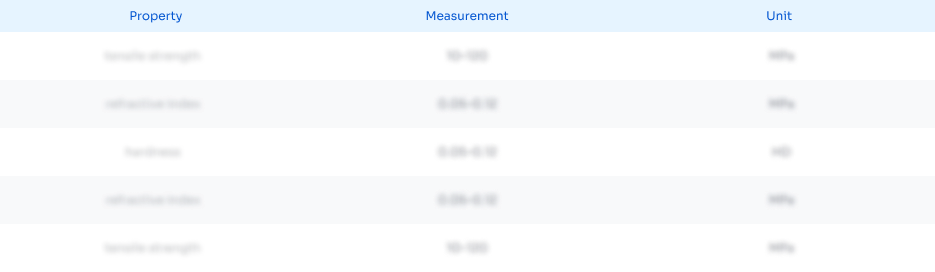
Abstract
Description
Claims
Application Information

- R&D
- Intellectual Property
- Life Sciences
- Materials
- Tech Scout
- Unparalleled Data Quality
- Higher Quality Content
- 60% Fewer Hallucinations
Browse by: Latest US Patents, China's latest patents, Technical Efficacy Thesaurus, Application Domain, Technology Topic, Popular Technical Reports.
© 2025 PatSnap. All rights reserved.Legal|Privacy policy|Modern Slavery Act Transparency Statement|Sitemap|About US| Contact US: help@patsnap.com