Low-odor scratch-resistant high-rigidity polypropylene composition and preparation method thereof
A composite material and polypropylene technology, which is applied in the field of polymer material processing, can solve the problems of high scratch resistance, high price, and poor comprehensive mechanical properties of automobile dashboards, and achieve excellent surface scratch resistance and low price. Low, good impact resistance effect
- Summary
- Abstract
- Description
- Claims
- Application Information
AI Technical Summary
Problems solved by technology
Method used
Image
Examples
Embodiment 1
[0035] Table 1
[0036] raw material
parts by mass
PP
80
20
[0037] Nano anti-scratch agent
0.1
Antioxidant 1010
1
Antioxidant 168
1
PTFE
2
1
[0038] In this case, the nano-scratch-resistant agent was compounded as nano-alumina: nano-silicon oxide: nano-zinc oxide = 50:30:20;
[0039] After weighing the materials according to the ratio in Table 1, follow the steps below to make the materials
[0040] (1) Add talcum powder and stir and mix for 4 minutes at a speed of 480 rpm;
[0041] (2) Add the nano anti-scratch agent and stir and mix for 9 minutes at a speed of 450 rpm;
[0042] (3) Stir and mix the polypropylene material with lubricant and antioxidant at a speed of 500 rpm for 5 minutes;
[0043] (4) Stir and mix for 10 minutes at a rotating speed of 1800 rpm;
[0044] (5). Stir for 10 minutes at a rotating speed of 350...
Embodiment 2
[0053] Table 4
[0054] raw material
[0055] In this case, the nano-scratch-resistant agent is compounded as nano-alumina: nano-silicon oxide: nano-zinc oxide = 40:40:20;
[0056] After weighing the materials according to the ratio in Table 4, follow the steps below to make the materials
[0057] (1) Add talcum powder and stir and mix for 4 minutes at a speed of 480 rpm;
[0058] (2) Add the nano anti-scratch agent and stir and mix for 9 minutes at a speed of 450 rpm;
[0059] (3) Stir and mix the polypropylene material with lubricant and antioxidant at a speed of 500 rpm for 5 minutes;
[0060] (4) Stir and mix for 10 minutes at a rotating speed of 1800 rpm;
[0061] (5) Stir for 10 minutes at a rotating speed of 350 rpm to obtain the initial mixture;
[0062] (6) Extruding and granulating the primary mixture through an extruder to obtain the final product.
[0063] Concrete process conditions are as shown in table 5:
[0064] table 5
[0065]
[0066] Th...
Embodiment 3
[0071] Table 7
[0072] raw material
parts by mass
PP
70
Talc powder
20
Nano anti-scratch agent
10
Antioxidant 1010
1
Antioxidant 168
1
PTFE
2
2
[0073] In this case, the nano-scratch-resistant agent is compounded as nano-alumina: nano-silicon oxide: nano-zinc oxide = 25:70:5;
[0074] After weighing the above-mentioned materials according to the ratio in Table 7, make the materials according to the following steps
[0075] (1) Add talcum powder and stir and mix for 4 minutes at a speed of 480 rpm;
[0076] (2) Add the nano anti-scratch agent and stir and mix for 9 minutes at a speed of 450 rpm;
[0077] (3) Stir and mix the polypropylene material with lubricant and antioxidant at a speed of 500 rpm for 5 minutes;
[0078] (4) Stir and mix for 10 minutes at a rotating speed of 1800 rpm;
[0079] (5) Stir for 10 minutes at a rotating speed of 350 r...
PUM
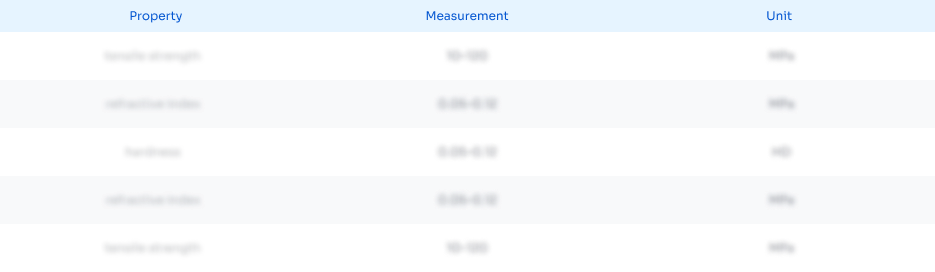
Abstract
Description
Claims
Application Information

- R&D
- Intellectual Property
- Life Sciences
- Materials
- Tech Scout
- Unparalleled Data Quality
- Higher Quality Content
- 60% Fewer Hallucinations
Browse by: Latest US Patents, China's latest patents, Technical Efficacy Thesaurus, Application Domain, Technology Topic, Popular Technical Reports.
© 2025 PatSnap. All rights reserved.Legal|Privacy policy|Modern Slavery Act Transparency Statement|Sitemap|About US| Contact US: help@patsnap.com