High-elasticity wear-resistant composite material
A composite material and high-elasticity technology, applied in the field of composite materials, can solve the problems of poor flexibility and rebound performance, poor softness and elasticity, and unsatisfactory wear resistance, so as to improve the rebound performance and flexibility , Improve compatibility and bonding, improve strength and wear resistance
- Summary
- Abstract
- Description
- Claims
- Application Information
AI Technical Summary
Problems solved by technology
Method used
Examples
specific Embodiment 1
[0019] A kind of highly elastic and wear-resistant rubber-plastic composite material adopts 20kg of talcum powder,
[0020] The coupling agent adopts 0.1kg of silane coupling agent, the metal oxide adopts 0.6kg of ZnO as foaming aid and active agent, and the lubricant adopts 0.2kg of stearic acid and 0.3kg of zinc stearate; foaming agent 4kg of AC azo foaming agent is used; 1kg of dicumyl peroxide is used as a bridging agent; the raw material of rubber particles is 100kg, and the ratio of raw materials of rubber particles is: 90kg of EVA (ethylene vinyl acetate), 5kg of POE (polyolefin elastomer), 4kg of EPDM rubber, 1kg of oil-extended (mineral oil) styrene-ethylene / butylene-styrene copolymer.
[0021] The production process of a high elastic wear-resistant rubber-plastic composite material is as follows: First, 90kg of EVA (ethylene vinyl acetate), 5kg of POE (polyolefin elastomer), 4kg of EPDM rubber, 1 kg of oil-extended (mineral oil) styrene-ethylene / butylene-styrene cop...
specific Embodiment 2
[0023] A kind of high elastic wear-resistant rubber-plastic composite material, adopts 2kg calcium carbonate as filler, coupling agent adopts 7kg titanate coupling agent, metal oxide adopts 2kg ZnO as foaming aid and activator, lubricating agent Agent adopts the stearic acid of 1kg and the zinc stearate of 1kg, foaming agent adopts the AC azo foaming agent of 0.5kg, bridging agent adopts the colloidal raw material of 0.4kg dicumyl peroxide, 100kg, its The ratio is: 60kg of EVA (ethylene vinyl acetate), 20kg of POE (polyolefin elastomer), 15kg of EPDM rubber, 5kg of oil-extended (mineral oil) styrene-ethylene / butylene-benzene Ethylene copolymer.
[0024] The production process of a high elastic wear-resistant rubber-plastic composite material is as follows: First, 60kg of EVA (ethylene vinyl acetate), 20kg of POE (polyolefin elastomer), 15kg of EPDM 5kg of oil-extended (mineral oil) styrene-ethylene / butylene-styrene copolymer with 2kg of talc, 2kg of ZnO, 1kg of stearic acid a...
specific Embodiment 3
[0026] A kind of high elasticity wear-resistant rubber-plastic composite material, adopts 15kg of talcum powder or calcium carbonate as the filler, 3kg of silane coupling agent or titanate coupling agent as the coupling agent, and 1kg of ZnO as the metal oxide. 0.7kg of stearic acid and 0.8kg of zinc stearate are used as foam aids and active agents, lubricants are used, 2kg of AC azo foaming agents are used as foaming agents, and 0.6kg of diisoperoxide is used as bridging agent Propylbenzene, 100kg of rubber particle raw materials, the ratio of rubber particle raw materials is: 50kg of EVA (ethylene vinyl acetate), 20kg of POE (polyolefin elastomer), 23kg of EPDM rubber, 7kg of oil-extended (mineral oil) styrene-ethylene / butylene-styrene copolymer.
[0027] The production process of a high elastic and wear-resistant rubber-plastic composite material is as follows: first, 50kg of EVA (ethylene vinyl acetate), 20kg of POE (polyolefin elastomer), 23kg of EPDM rubber, 7 kg of oil...
PUM
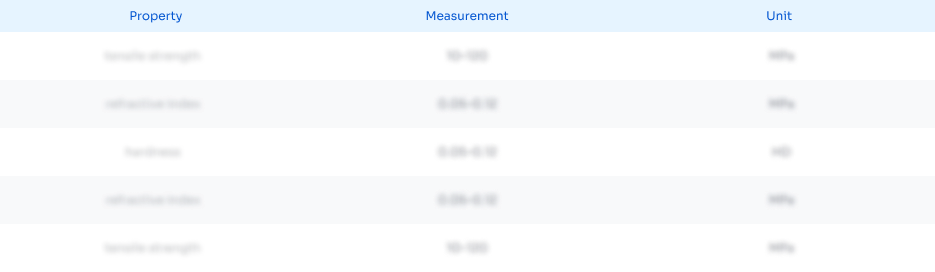
Abstract
Description
Claims
Application Information

- R&D Engineer
- R&D Manager
- IP Professional
- Industry Leading Data Capabilities
- Powerful AI technology
- Patent DNA Extraction
Browse by: Latest US Patents, China's latest patents, Technical Efficacy Thesaurus, Application Domain, Technology Topic, Popular Technical Reports.
© 2024 PatSnap. All rights reserved.Legal|Privacy policy|Modern Slavery Act Transparency Statement|Sitemap|About US| Contact US: help@patsnap.com