Method for preparing inorganic refractory fiber product from thermal-state pulverized fuel ash or slag
A technology of inorganic refractory fiber and fly ash, applied in manufacturing tools, glass manufacturing equipment, etc., can solve the problems of increased production cost of high-temperature refractory fiber products, difficult production to meet demand, and restricted demand, so as to reduce raw material procurement and transportation costs , low cost of local use, and the effect of reducing environmental pollution
- Summary
- Abstract
- Description
- Claims
- Application Information
AI Technical Summary
Problems solved by technology
Method used
Examples
Embodiment 1
[0027] (1) All fly ash is used as raw material. The main components and contents of fly ash are: Al2O3: 33% -36%, SiO2: 43% - 50%, CaO: 5% -10%.
[0028] Directly connect the propeller pipeline from the standby slag removal channel. Multiple propellers can be installed in the pipeline according to the specific situation, which can be climbed, turned or placed in the trench. All pipelines must be made of stainless steel and external insulation measures should be taken . The propeller selects the tubular screw conveyor suitable for muck transportation.
[0029] (2) Raw material melting: Connect the spare slag outlet of the existing boiler to the propeller, and transport the hot slag directly to the resistance melting furnace through a fully sealed pipeline. The resistance furnace uses a three-phase molybdenum electrode as a heating element. After the molten material is heated and melted, it conducts to form a circuit and forms a molten pool of a certain size. After the melting...
Embodiment 2
[0037] (1) All use slag as raw material. The main components and contents of slag are: Al2O3: 30% -33%, SiO2: 50% - 53%, CaO: 3% -5.5%.
[0038] (2) Raw material melting: The resistance furnace uses three-phase molybdenum electrodes as the heating element, and the molten material is heated and melted to form a circuit, and the resistance of the molten material itself is used to continue heating and melting the raw material to form a melt of suitable size suitable for high-temperature melt discharge. pool.
[0039] (3) When the molten pool is discharged, the molten pool is discharged from the hole in the middle of the tungsten or molybdenum nozzle at the bottom of the furnace to form a liquid stream, which flows out by the gravity of the stream itself.
[0040] (4) Cotton collection: The conveying net plate of the cotton collector is cleaned with a dry brush. The cotton collecting machine can run at an adjustable speed, and the cotton felt with a certain thickness and uniform...
Embodiment 3
[0046] (1) Mix half of fly ash and slag as raw material. The main components after mixing hot slag and fly ash are: Al2O3: 30% -35%, SiO2: 45% - 50%, CaO: 5% -10%, and the acidity coefficient of the material is 4.75.
[0047] (2) Raw material melting: The hot slag is directly transported to the resistance melting furnace through a fully sealed pipeline. The resistance furnace uses a three-phase molybdenum electrode as a heating element. After the molten material is heated and melted, it is conducted to form a circuit, and the raw material is continuously heated and melted to form a molten pool with a suitable size for high-temperature melt discharge.
[0048] (3) When the molten pool is discharged, the molten pool is discharged from the hole in the middle of the tungsten or molybdenum nozzle at the bottom of the furnace to form a liquid stream, which flows out by the gravity of the stream itself.
[0049] (4) Cotton collection: The conveying net plate of the cotton collector ...
PUM
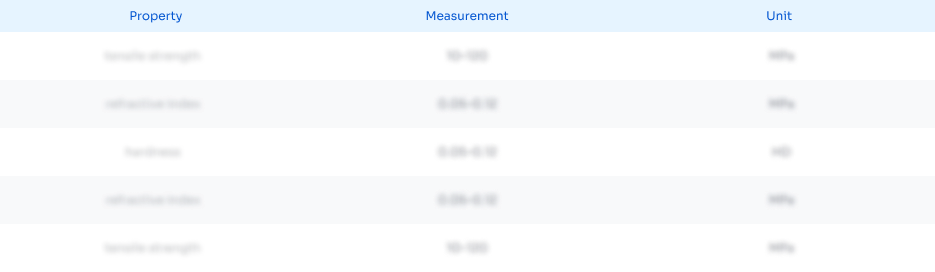
Abstract
Description
Claims
Application Information

- R&D
- Intellectual Property
- Life Sciences
- Materials
- Tech Scout
- Unparalleled Data Quality
- Higher Quality Content
- 60% Fewer Hallucinations
Browse by: Latest US Patents, China's latest patents, Technical Efficacy Thesaurus, Application Domain, Technology Topic, Popular Technical Reports.
© 2025 PatSnap. All rights reserved.Legal|Privacy policy|Modern Slavery Act Transparency Statement|Sitemap|About US| Contact US: help@patsnap.com