Polypropylene material with paint spraying effect and preparation method for polypropylene material
A polypropylene material and polypropylene technology are applied in the field of polypropylene material with paint spraying effect and its preparation, which can solve the problems of increasing automobile manufacturing cost, polluting the environment, etc. easy-to-control effects
- Summary
- Abstract
- Description
- Claims
- Application Information
AI Technical Summary
Problems solved by technology
Method used
Image
Examples
Embodiment 1
[0038] Graft 80 kg of polypropylene, 0.5 kg of phenolic heat stabilizer Irganox 1010 (CIBA company), 0.5 kg of lubricant calcium stearate, 5 kg of toughening agent high-density polyethylene, and 2 kg of interface compatibilizer polypropylene Toric anhydride, 10 kilograms of mineral powder calcium carbonate and 2 kilograms of superfine aluminum powder are melted, mixed and dispersed in a twin-screw extruder with a length-to-diameter ratio of 40:1, extruded and granulated to obtain the polypropylene material of this embodiment . The processing temperature in the above process was 200°C.
[0039] The polypropylene material obtained in this example has a paint-like appearance, excellent scratch resistance and good comprehensive mechanical properties. The specific test results are as follows:
[0040]
[0041] *PV3952 is the scratch standard of Volkswagen AG.
Embodiment 2
[0043] 74 kg of polypropylene, 0.5 kg of phenolic heat stabilizer Irganox 1010 (CIBA company), 0.5 kg of lubricant calcium stearate, 9 kg of toughening agent ethylene-octene copolymer, 3 kg of interface compatibilizer polypropylene Branched maleic anhydride, 12 kilograms of mineral powder talcum powder and 1 kilogram of superfine aluminum powder are melt mixed and dispersed in a twin-screw extruder with a length-to-diameter ratio of 40:1, extruded and granulated, and obtained the polymer of the present embodiment. Acrylic material. The processing temperature in the above process was 200°C.
[0044] The polypropylene material obtained in this example has a paint-like appearance, excellent scratch resistance and good comprehensive mechanical properties. The specific test results are as follows:
[0045]
Embodiment 3
[0047] 52 kg of polypropylene, 0.5 kg of phenolic heat stabilizer Irganox 1010 (CIBA company), 1 kg of lubricant calcium stearate, 12 kg of toughening agent ethylene-octene copolymer, 3 kg of interface compatibilizer polypropylene Branched maleic anhydride, 30 kilograms of mineral powder talcum powder and 1.5 kilograms of superfine aluminum powder are melt mixed and dispersed in a twin-screw extruder with a length-to-diameter ratio of 40:1, extruded and granulated to obtain the poly Acrylic material. The processing temperature in the above process was 200°C.
[0048] The polypropylene material obtained in this example has a paint-like appearance, excellent scratch resistance and good comprehensive mechanical properties. The specific test results are as follows:
[0049]
[0050] The polypropylene material with paint spraying effect of the present invention can be used to make automotive exterior products that require paint spraying, such as automobile bumpers, heat d...
PUM
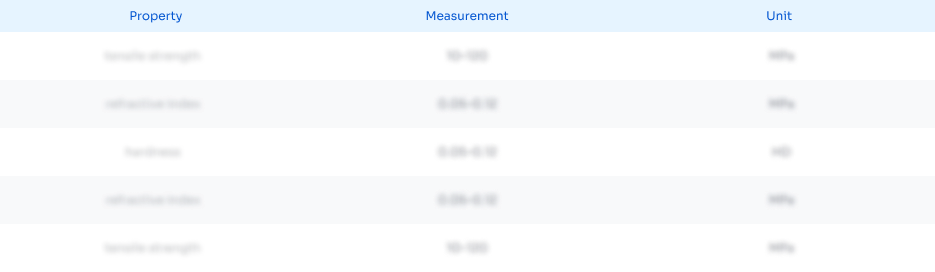
Abstract
Description
Claims
Application Information

- R&D
- Intellectual Property
- Life Sciences
- Materials
- Tech Scout
- Unparalleled Data Quality
- Higher Quality Content
- 60% Fewer Hallucinations
Browse by: Latest US Patents, China's latest patents, Technical Efficacy Thesaurus, Application Domain, Technology Topic, Popular Technical Reports.
© 2025 PatSnap. All rights reserved.Legal|Privacy policy|Modern Slavery Act Transparency Statement|Sitemap|About US| Contact US: help@patsnap.com