Preparation method for anti-reflective glass
A technology of anti-reflection glass and silicate glass, applied in the field of anti-reflection glass, can solve the problems of low laser damage threshold, narrow anti-reflection band, limited application prospects of anti-reflection optical glass, etc. Laser damage threshold and anti-reflection wavelength controllable effect
- Summary
- Abstract
- Description
- Claims
- Application Information
AI Technical Summary
Problems solved by technology
Method used
Image
Examples
preparation example Construction
[0030] The preparation method of the anti-reflection glass of the present invention comprises the following steps:
[0031] ①Use deionized water, alkaline cleaner, and deionized water to ultrasonically clean the silicate glass substrate for 5 to 10 minutes, and place it in a clean room to dry naturally;
[0032] ② Using a nanosecond laser with a wavelength of 1064nm to perform "grid scanning" laser pretreatment on the glass surface, the energy density of the nanosecond laser with a wavelength of 1064nm ranges from 20% to 60% of the glass laser damage threshold;
[0033] ③ Immerse the laser-pretreated glass substrate in an etching solution, and perform etching treatment at a temperature of 85°C to 90°C for 10 to 40 hours;
[0034] ④ Finally, the etched glass substrate is ultrasonically cleaned with deionized water, alkaline cleaning agent, and deionized water for 5 to 10 minutes respectively, and then heated and dried to obtain anti-reflection glass.
[0035] 2. The method for...
Embodiment 1
[0039] 1. Cleaning: Use deionized water, alkaline cleaning agent, and deionized water to ultrasonically clean the silicate glass substrate for 5 to 10 minutes; dry naturally in the clean room atmosphere;
[0040] 2. Use 1064nm, 12ns laser pulses to perform "grid scanning" pretreatment on the surface of the silicate glass substrate, and the incident laser energy density at 0 degrees is 9J / cm 2 , the spot area is 0.09mm 2 , real-time monitoring of the processing process;
[0041] 3. Prepare 0.03mol / L Na 2 HPO 4 : 0.001mol / L AlCl 3 =1:1 mixed solution as etching solution;
[0042] 4. Etching: immerse the silicate glass substrate in an etching solution at a constant temperature of 85°C for 10 hours;
[0043] 5. Cleaning: Take the silicate glass substrate out of the solution, use deionized water, alkaline cleaning agent, and deionized water to ultrasonically clean the glass for 5-10 minutes, heat and dry to obtain anti-reflection glass;
[0044] 6. Spectrum measurement: The o...
Embodiment 2
[0046] 1. Cleaning: Use deionized water, alkaline cleaning agent, and deionized water to ultrasonically clean the silicate glass substrate for 5 to 10 minutes; dry naturally in the clean room atmosphere;
[0047] 2. Use 1064nm, 12ns laser pulses to perform "grid scanning" pretreatment on the surface of the silicate glass substrate, and the incident laser energy density at 0 degrees is 17J / cm 2 , the spot area is 0.09mm 2 , real-time monitoring of the processing process;
[0048] Steps 3-6 in Example 1 were repeated.
PUM
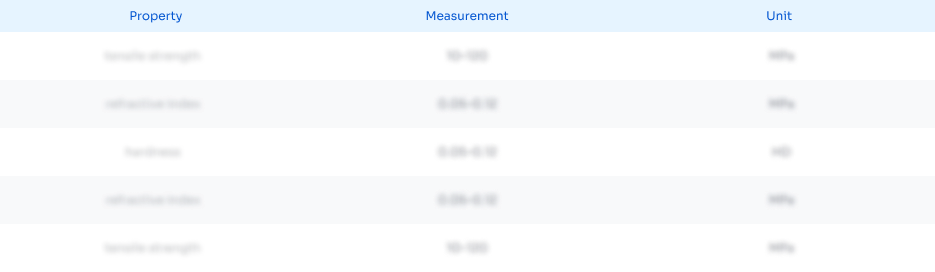
Abstract
Description
Claims
Application Information

- R&D
- Intellectual Property
- Life Sciences
- Materials
- Tech Scout
- Unparalleled Data Quality
- Higher Quality Content
- 60% Fewer Hallucinations
Browse by: Latest US Patents, China's latest patents, Technical Efficacy Thesaurus, Application Domain, Technology Topic, Popular Technical Reports.
© 2025 PatSnap. All rights reserved.Legal|Privacy policy|Modern Slavery Act Transparency Statement|Sitemap|About US| Contact US: help@patsnap.com