Free-machining pinion steel smelting method and free-machining pinion steel
A gear steel and free-cutting technology, which is applied in the field of smelting free-cutting gear steel, can solve the problems of lowering the purity of molten steel, increasing production costs, and generating inclusions, and achieves the effect of reducing production costs.
- Summary
- Abstract
- Description
- Claims
- Application Information
AI Technical Summary
Problems solved by technology
Method used
Examples
Embodiment 1
[0022] Using vanadium-extracted semi-steel as raw material, the mass percentages of its main components are: C: 3.50%, Mn: 0.04%, Cr: 0.04%, P: 0.04%, S: 0.07%, V: 0.035%, Fe: 96.27%, and the balance is impurities.
[0023] The semi-steel is blended into the compound blowing steelmaking converter for blowing, and a 536 oxygen lance is used for oxygen supply, slagging, dephosphorization and decarburization. At the same time as the oxygen blowing is started, the steelmaking slag is carried out and all the slagging materials are added within 6 minutes after the oxygen blowing is started. Slag-making materials include active lime, composite slagging agent, high-magnesium lime and steelmaking sludge balls, and the addition amounts are 31Kg / t semi-steel, 20Kg / t semi-steel, 18Kg / t semi-steel and 2.7Kg / t semi-steel . Wherein the mass percent of each component of active lime is: CaO: 96%, SiO 2 : 0.391%, MgO: 3.25%, and the balance is impurities; wherein the mass percentage of each ...
Embodiment 2
[0028] Smelting is carried out using the method of Example 1, wherein the mass percentages of the semi-steel used for primary smelting are: C: 3.8%, Mn: 0.02%, Cr: 0.045%, P: 0.05%, S: 0.085%, V: 0.028%, Fe: 95.97%, and the balance is impurities.
[0029] The semi-steel is blended into the compound blowing steelmaking converter for blowing, and a 536 oxygen lance is used for oxygen supply, slagging, dephosphorization and decarburization. At the same time as the oxygen blowing is started, the steelmaking slag is carried out and all the slagging materials are added within 6 minutes after the oxygen blowing is started. The slagging materials include active lime, composite slagging agent, high-magnesium lime and steelmaking sludge balls, and the addition amounts are 36Kg / t semi-steel, 21Kg / t semi-steel, 19Kg / t semi-steel and 2.9Kg / t semi-steel . When the oxygen supply time is 900 seconds, the oxygen supply is stopped and the oxygen lance is raised. The final basicity of the conv...
Embodiment 3
[0034] Smelting is carried out using the method of Example 1, wherein the mass percentages of the semi-steel used for primary smelting are: C: 3.70%, Mn: 0.07%, Cr: 0.06%, P: 0.07%, S: 0.12%, V: 0.031%, Fe: 95.94%, and the balance is impurities.
[0035] The semi-steel is blended into the compound blowing steelmaking converter for blowing, and a 536 oxygen lance is used for oxygen supply, slagging, dephosphorization and decarburization. At the same time as the oxygen blowing is started, the steelmaking slag is carried out and all the slagging materials are added within 6 minutes after the oxygen blowing is started. Slag-making materials include active lime, composite slagging agent, high-magnesium lime and steelmaking sludge balls, and the addition amounts are 38Kg / t semi-steel, 20Kg / t semi-steel, 19Kg / t semi-steel and 2.5Kg / t semi-steel . When the oxygen supply time is 920 seconds, the oxygen supply is stopped and the oxygen lance is raised. The final basicity of the conver...
PUM
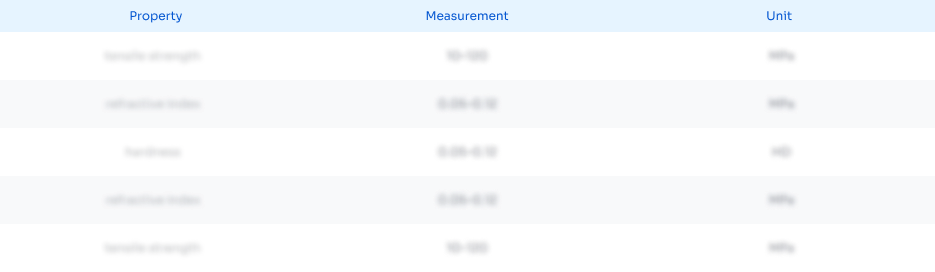
Abstract
Description
Claims
Application Information

- Generate Ideas
- Intellectual Property
- Life Sciences
- Materials
- Tech Scout
- Unparalleled Data Quality
- Higher Quality Content
- 60% Fewer Hallucinations
Browse by: Latest US Patents, China's latest patents, Technical Efficacy Thesaurus, Application Domain, Technology Topic, Popular Technical Reports.
© 2025 PatSnap. All rights reserved.Legal|Privacy policy|Modern Slavery Act Transparency Statement|Sitemap|About US| Contact US: help@patsnap.com