Preparation method of WC-Co hard alloy with average grain size larger than 15 microns
An average grain size, hard alloy technology, applied in metal processing equipment, transportation and packaging, etc., can solve the problems of lack of carbon phase, high sintering temperature, short ball milling time, etc., to promote the increase of fluidity and pore distribution Uniform, uniform temperature distribution effect
- Summary
- Abstract
- Description
- Claims
- Application Information
AI Technical Summary
Problems solved by technology
Method used
Image
Examples
Embodiment 1
[0028] Example 1: The goal is to prepare WC-15wt.%Co cemented carbide bulk material. Mix the tungsten carbide powder passed through a 500-mesh sieve with a mixed solution of PEG and diffusion oil at a volume ratio of 9:1. Each 100g of WC powder corresponds to 10ml of the mixed solution. After drying for 30 minutes, under a pressure of 300MPa (keep 10s) Carrying out cold pressing, covering and compacting the upper and lower surfaces of the cold-pressed compact with Co powder, placing it in a crucible, and putting it into a low-pressure sintering furnace for sintering. Raise the temperature from room temperature to 200°C at a rate of 4°C / min, keep it warm for 30 minutes, and discharge the gas adsorbed in the powder; continue to raise the temperature to 450°C, feed hydrogen, and keep it warm for 30 minutes to ensure that PEG and diffusion oil are completely discharged; continue to rise to 800°C in turn ℃ and 1230℃ respectively for 30 minutes to ensure that the temperature distrib...
Embodiment 2
[0029] Example 2: The goal is to prepare WC-10wt.%Co cemented carbide bulk material. Mix the tungsten carbide powder passed through a 500-mesh sieve with a mixture of prepared PEG and diffusion oil at a ratio of 9:1, dry for 30 minutes, and perform cold pressing under a pressure of 300 MPa (holding for 10 seconds). The billet is pre-sintered in a low-pressure sintering system. The specific process is: raise the temperature from room temperature to 270°C at a rate of 4°C / min, and keep it for 40 minutes; The speed was increased to 1450°C for 30 minutes, and the furnace was cooled to room temperature to prepare porous tungsten carbide; after the upper and lower surfaces of porous tungsten carbide were covered with Co powder and compacted, they were placed in a crucible and sintered in a low-pressure sintering furnace. The process is as follows: heat up from room temperature to 1230°C at a rate of 4°C / min, pass in hydrogen and keep warm for 60 minutes; heat up to 1480°C at a rate ...
Embodiment 3
[0030]Example 3: The goal is to prepare WC-8wt.%Co cemented carbide bulk material. Mix the tungsten carbide powder passed through a 800-mesh sieve with a mixture of prepared PEG and diffusion oil at a ratio of 10:1, dry for 30 minutes, and perform cold pressing under a pressure of 350 MPa (holding for 10 seconds). The billet is pre-sintered in a low-pressure sintering system. The specific process is: raise the temperature from room temperature to 250°C at a rate of 4°C / min, and keep it for 30 minutes; The speed was increased to 1500°C for 30 minutes, and then cooled to room temperature with the furnace to prepare porous tungsten carbide; after the upper and lower surfaces of porous tungsten carbide were covered with Co powder and compacted, they were placed in a crucible and sintered in a low-pressure sintering furnace. The specific process is as follows: heat up from room temperature to 1250°C at a rate of 4°C / min, pass in hydrogen, and keep warm for 40 minutes; heat up to 15...
PUM
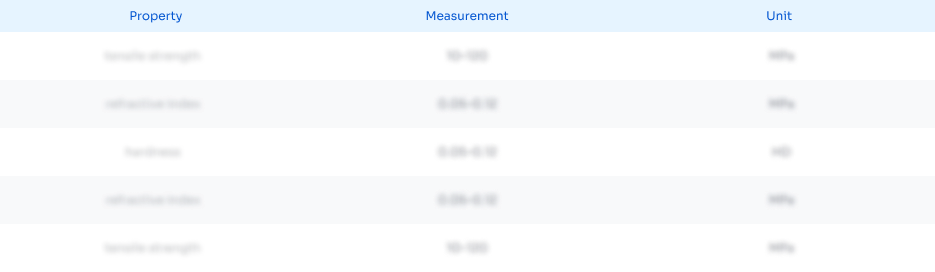
Abstract
Description
Claims
Application Information

- R&D
- Intellectual Property
- Life Sciences
- Materials
- Tech Scout
- Unparalleled Data Quality
- Higher Quality Content
- 60% Fewer Hallucinations
Browse by: Latest US Patents, China's latest patents, Technical Efficacy Thesaurus, Application Domain, Technology Topic, Popular Technical Reports.
© 2025 PatSnap. All rights reserved.Legal|Privacy policy|Modern Slavery Act Transparency Statement|Sitemap|About US| Contact US: help@patsnap.com