Flameretardant conveyor belt for aramid fiber core
A conveyor belt and aramid technology, applied in the field of aramid core flame retardant conveyor belt, can solve the problems of large diameter of the driving roller, difficult to manufacture the whole core conveyor belt, and the weight of the steel wire rope belt, so as to achieve light weight, Small diameter and good corrosion resistance
- Summary
- Abstract
- Description
- Claims
- Application Information
AI Technical Summary
Problems solved by technology
Method used
Image
Examples
Embodiment 1
[0032] Such as figure 1 As shown, the present invention consists of an upper flame-retardant covering rubber layer 1, a flame-retardant adhesive glue 2, a buffer layer 3, an aramid fiber skeleton layer 4, and a lower flame-retardant covering rubber layer 5. A buffer layer 3 is arranged on both sides of the aramid skeleton layer 4, and the two sides of the aramid skeleton layer 4 and the buffer layer 3 are pasted with flame-retardant adhesive glue 2, and the aramid skeleton layer 4 and the buffer layer 3 are bonded by flame-retardant The glue 2 is bonded, and the buffer layer 3 is glued to the upper flame-retardant covering glue layer 1 and the lower flame-retardant covering glue layer 5 through the flame-retardant adhesive glue.
[0033] figure 2 It is a schematic diagram of the structure of the aramid fiber skeleton layer with two layers of warps. In the figure, the first and second rows of weft C, warp A and connecting wires 1A and 2A constitute a straight warp conveyor b...
Embodiment 2
[0036] The aramid fiber skeleton layer 3 uses a double-layer structure canvas with straight warp and straight weft, the specification model is DEP2800, and the buffer layer 3 uses ordinary nylon 66 mesh cloth.
[0037] Flame retardant cover layer rubber formula, its ratio by weight: 100 parts of neoprene; 4 parts of zinc oxide, 5 parts of magnesium oxide; 0.5 parts of accelerator NA-22; 35 parts of super wear-resistant N220 carbon black, high Mill N330 carbon black 15 parts; decabromodiphenyl ether 10 parts, chlorinated paraffin-70 20 parts, antimony trioxide 10 parts, colloidal red phosphorus 8 parts, flame retardant lubricant MB202 15 parts.
[0038] Flame retardant laminating rubber compound formula, its ratio by weight: 60 parts of natural rubber, 25 parts of styrene-butadiene rubber, 15 parts of butadiene rubber; 1.0 parts of accelerator CZ, 1.5 parts of accelerator DM; 8 parts of zinc oxide; anti-aging agent 1.5 parts of 4010NA, 1.5 parts of anti-aging agent RD; 15 parts...
Embodiment 3
[0047] The aramid skeleton layer 3 uses DEP-800 straight warp and straight weft single-layer canvas, and the cushioning material is nylon polyester dipped canvas.
[0048] Flame retardant overlay compound formula, its ratio by weight:
[0049] 90 parts of chloroprene rubber, 10 parts of butadiene rubber, 2.5 parts of nano zinc oxide, 3 parts of activated magnesium oxide, 45 parts of N220 carbon black, 8 parts of decabromodiphenyl ether, 17 parts of chlorinated paraffin, 8 parts of antimony trioxide Parts, 15 parts of zinc borate, 12 parts of ammonium polyphosphate.
[0050] Flame retardant lamination adhesive formula, its proportion by weight:
[0051] 50 parts of natural rubber, 50 parts of styrene-butadiene rubber; 5 parts of zinc oxide; 1.0 parts of accelerator CZ, 1.7 parts of accelerator DM; 2 parts of anti-aging agent BLE, 1 part of anti-aging agent 4010NA; 15 parts of paraffin wax, 7 parts of antimony trioxide, 11 parts of ammonium polyphosphate, 17 parts of aluminum ...
PUM
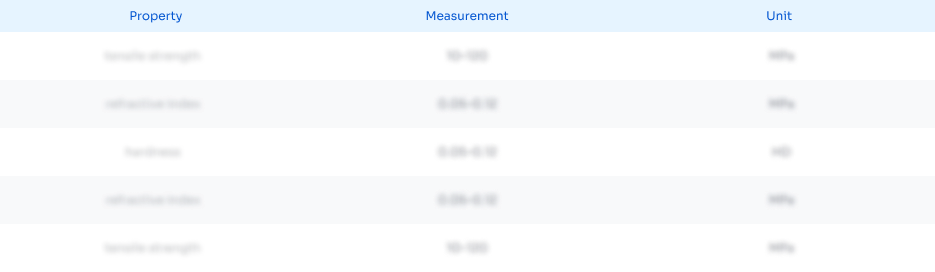
Abstract
Description
Claims
Application Information

- R&D
- Intellectual Property
- Life Sciences
- Materials
- Tech Scout
- Unparalleled Data Quality
- Higher Quality Content
- 60% Fewer Hallucinations
Browse by: Latest US Patents, China's latest patents, Technical Efficacy Thesaurus, Application Domain, Technology Topic, Popular Technical Reports.
© 2025 PatSnap. All rights reserved.Legal|Privacy policy|Modern Slavery Act Transparency Statement|Sitemap|About US| Contact US: help@patsnap.com