Method of ultra-low-carbon steel dephosphorization outside furnace
An extra-furnace dephosphorization and ultra-low carbon steel technology, which is applied in the field of steelmaking technology, can solve the problems affecting the qualified rate of steel quality and economic benefits, the difficulty of converter smelting control, and the impact on product delivery rate, so as to reduce the accident of steel modification and economic loss, improving thermodynamic and kinetic conditions, and achieving effective control
- Summary
- Abstract
- Description
- Claims
- Application Information
AI Technical Summary
Problems solved by technology
Method used
Examples
Embodiment 1
[0014] 260t converter, 260t ladle and 260tLF furnace are used to produce ultra-low carbon steel, and the process flow is executed in sequence of converter, LF furnace and RH furnace. The specific measures and methods are:
[0015] 1. Lower the tapping target temperature of the converter, and control the tapping target temperature at 1680°C.
[0016] 2. During the tapping process of the converter, add 800kg of small grains of lime into the ladle.
[0017] 3. When the molten steel enters the refining process of the LF furnace, 700kg of lime and 150kg of refining slag are added to heat up the slag; the temperature compensation is controlled according to the target temperature of 1630°C.
[0018] 4. After the temperature rise is completed and the slag has been fully melted, the argon gas flow rate is 40Nm 3 / h, carry out argon blowing and stirring, and the stirring time is 5min. Dephosphorization is carried out with high alkalinity, good fluidity and good stirring dynamics.
Embodiment 2
[0020] 260t converter, 260t ladle and 260tLF furnace are used to produce ultra-low carbon steel, and the process flow is executed in sequence of converter, LF furnace and RH furnace. The specific measures and methods are:
[0021] 1. Reduce the tapping target temperature of the converter, and control the tapping target temperature at 1670°C.
[0022] 2. During the tapping process of the converter, add 600kg of small grains of lime into the ladle.
[0023] 3. When the molten steel enters the refining process of the LF furnace, 800kg of lime and 200kg of refining slag are added to heat up the slag; the temperature compensation is controlled according to the target temperature of 1630°C.
[0024] 4. After the temperature rise is completed and the slag has been fully melted, the flow rate of argon gas is 75Nm 3 / h, carry out argon blowing and stirring, and the stirring time is 3min. Dephosphorization is carried out with high alkalinity, good fluidity and good stirring dynamics....
PUM
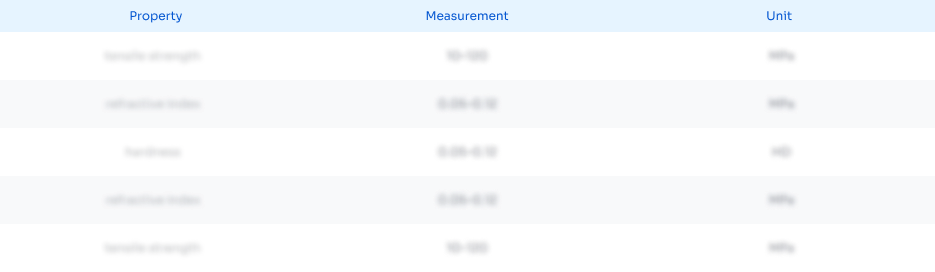
Abstract
Description
Claims
Application Information

- R&D
- Intellectual Property
- Life Sciences
- Materials
- Tech Scout
- Unparalleled Data Quality
- Higher Quality Content
- 60% Fewer Hallucinations
Browse by: Latest US Patents, China's latest patents, Technical Efficacy Thesaurus, Application Domain, Technology Topic, Popular Technical Reports.
© 2025 PatSnap. All rights reserved.Legal|Privacy policy|Modern Slavery Act Transparency Statement|Sitemap|About US| Contact US: help@patsnap.com