Bimetal or multi-metal high-dispersion composite coal tar hydrogenation catalyst and preparation method thereof
A hydrogenation catalyst and multi-metal technology, which is applied in the field of bimetallic or multi-metal highly dispersed composite coal tar hydrogenation catalyst and its preparation, can solve the problems of low catalyst hydrogenation activity, affecting product yield and quality, etc., to reduce Preparation cost, improvement of utilization rate, effect of high dispersibility
- Summary
- Abstract
- Description
- Claims
- Application Information
AI Technical Summary
Problems solved by technology
Method used
Image
Examples
Embodiment 1
[0020] Example 1: Catalyst preparation
[0021] In this example, a kind of Chinese bituminous coal was used as the carrier coal for preparing the catalyst, and FeSO heptahydrate was taken 4 6.00 kg, add 47.00 kg of fresh water to dissolve, then add 15.00 kg of bituminous coal powder with a particle diameter of 100μm, stir evenly to prepare FeSO 4 Coal slurry, another 1.30 kg of concentrated ammonia water is added to 17.5 kg of fresh water to prepare an ammonia solution, and the above ammonia solution is added to the above FeSO under stirring 4 In the coal slurry, continue to stir for 10 minutes after the addition, the PH value at the end of the reaction is 7.7, the reaction product Fe(OH) 2 Loaded on coal powder. Put the above reaction product at 40℃, 3m 3 / h Air flow oxidation for 100 minutes. After the oxidation reaction is completed, Fe(OH) 2 It is oxidized to γ-FeOOH and subjected to centrifugal filtration to obtain a filter cake. Then, take 0.082 kg of 10% by mass ammonium m...
Embodiment 2
[0022] Example 2: Catalyst preparation
[0023] The preparation process of Example 2 is the same as that of Example 1, except that the 10% by mass ammonium molybdate aqueous solution in Example 1 is a nickel carbonate ammonia aqueous solution containing 10% by mass nickel carbonate, and the spray amount is approximately equal to the mass ratio of nickel: iron 1:400. The powdered catalyst with a water content of less than 4% (mass) obtained by drying is the catalyst of the present invention. The Fe content of the catalyst is 7.2% (mass), the dry coal content is 90.0% (mass), and the nickel content is 0.02% (mass).
Embodiment 3
[0024] Example 3: Example 3 has the same preparation process as Example 1, except that the 10% by mass aqueous solution of ammonium molybdate in Example 1 is a 10% by mass aqueous solution of cobalt nitrate, and the spray amount is approximately equal to the mass ratio of cobalt to iron 1:400. The powdered catalyst with a water content of less than 4% (mass) obtained by drying is the catalyst of the present invention. The Fe content of the catalyst is 7.3% (mass), the dry coal content is 89.0% (mass), and the cobalt content is 0.02% (mass).
PUM
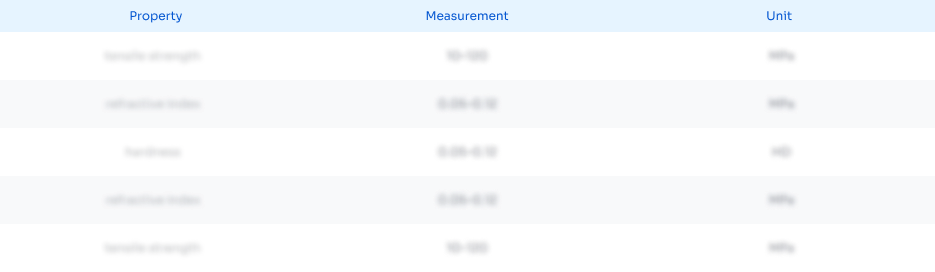
Abstract
Description
Claims
Application Information

- R&D
- Intellectual Property
- Life Sciences
- Materials
- Tech Scout
- Unparalleled Data Quality
- Higher Quality Content
- 60% Fewer Hallucinations
Browse by: Latest US Patents, China's latest patents, Technical Efficacy Thesaurus, Application Domain, Technology Topic, Popular Technical Reports.
© 2025 PatSnap. All rights reserved.Legal|Privacy policy|Modern Slavery Act Transparency Statement|Sitemap|About US| Contact US: help@patsnap.com