Method for preparing multi-component composite oxide catalyst for denitration by metal plate
A denitration catalyst and multi-component composite technology, which is applied in the field of catalyst preparation, can solve the problems of non-regeneration of deactivated catalyst waste residue, high investment cost and operating cost, uneven distribution of active components, etc. The effect of good sintering resistance
- Summary
- Abstract
- Description
- Claims
- Application Information
AI Technical Summary
Problems solved by technology
Method used
Image
Examples
Embodiment 1
[0025] First remove the surface oxide of the stainless steel plate in 0.1 M HCl, then degrease in 0.15 M NaOH, ultrasonically treat in isopropanol for 10 min, vacuum dry, and set aside;
[0026] Take 0.1 mol / L Ni(NO 3 ) 2 , 0.5 mol / L NH 4 Cl and 0.001 mol / L sodium citrate 200 ml, adjust the pH value to 6.5 with 10% ammonia solution. Put the treated stainless steel plate vertically into the mixed salt solution, and transfer it to a polytetrafluoro-lined autoclave, 150 o C water heat for 12 h. The stainless steel plate on which the double metal hydroxide film was grown in situ was washed with deionized water and dried. Put the obtained stainless steel plate into the muffle furnace and program the temperature from room temperature to 500 o C, calcined for 5 h to obtain the final product. from figure 1 It can be seen that the composite oxides obtained after calcination still maintain orderly arrangement.
[0027] The method for testing the SCR activity of the prepared cata...
Embodiment 2
[0029] First remove the surface oxide of the copper plate in 0.1 M HCl, then degrease in 0.15 M NaOH, ultrasonically treat in isopropanol for 10 min, vacuum dry, and set aside;
[0030] Take 0.2 mol / L Ce(NO 3 ) 2 , 2 mol / L NH 4 Cl and 0.05 mol / L sodium citrate 300 ml, adjust the pH value to 7 with 10% ammonia solution. Put the treated copper plate vertically into the mixed salt solution, and transfer it to a polytetrafluoro-lined autoclave, 180 oC water heat for 24 h. The copper plate on which the double metal hydroxide film was grown in situ was washed with deionized water and dried. Put the obtained copper plate into the muffle furnace and program the temperature from room temperature to 500 o C, calcined for 5 h to obtain the final product
[0031] Activity test method is the same as embodiment 1, at reaction temperature 250 o C.C NO =C NH3 =550 ppm, C O2 =3%, space velocity=30000 h -1 Under operating conditions, the catalytic reduction efficiency of the catalyst...
Embodiment 3
[0033] According to the preparation method of the present invention in Example 1, the stainless steel plate of the (uncalcined) double metal hydroxide film obtained by in-situ growth was immersed in an ammonium metavanadate solution with an ion concentration of 0.2 M for 10 s and taken out for 100 o C drying, dipping into the ammonium metavanadate solution again, repeating five times. Put the stainless steel plate with ammonium metavanadate into the muffle furnace and program the temperature from room temperature to 500 o C, calcined for 6 h to obtain the final product.
[0034] Activity test method is the same as embodiment 1, at reaction temperature 300 o C.C NO =C NH3 =550 ppm, C O2 =3%, space velocity=30000 h -1 Under operating conditions, the catalytic reduction efficiency of the catalyst can be kept above 85% for a long time.
PUM
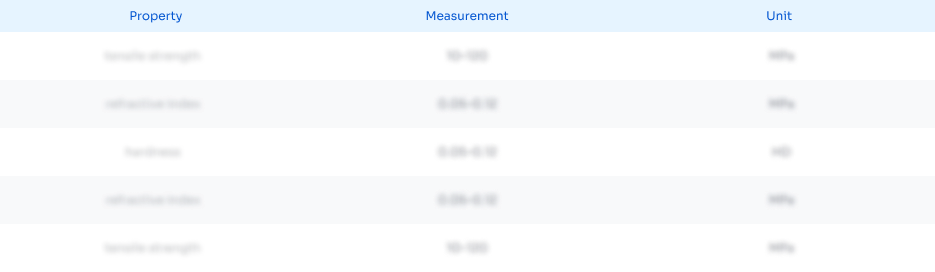
Abstract
Description
Claims
Application Information

- R&D
- Intellectual Property
- Life Sciences
- Materials
- Tech Scout
- Unparalleled Data Quality
- Higher Quality Content
- 60% Fewer Hallucinations
Browse by: Latest US Patents, China's latest patents, Technical Efficacy Thesaurus, Application Domain, Technology Topic, Popular Technical Reports.
© 2025 PatSnap. All rights reserved.Legal|Privacy policy|Modern Slavery Act Transparency Statement|Sitemap|About US| Contact US: help@patsnap.com