Resin composition and processed paper or fiber product treated therewith
A resin composition and monomer technology, applied in fiber processing, fiber raw material processing, papermaking, etc., can solve the problems of reduced design, uncontrollable bending resistance, inability to meet strength and bending resistance, etc., and achieve excellent bending resistance. sexual effect
- Summary
- Abstract
- Description
- Claims
- Application Information
AI Technical Summary
Problems solved by technology
Method used
Image
Examples
Embodiment 1
[0052] 150 g of ion-exchanged water was put into a 1 L five-necked detachable flask, and heated to 80° C. while stirring. 36 g of ethyl acrylate, 36 g of methyl methacrylate, 18 g of acrylic acid, and 60 g of polyoxyethylene glycol monomethacrylic acid phosphate (manufactured by Kyoeisha Chemical Co., Ltd., Laitester P-1M, phosphorus content 15% by mass) , 1.5 g of sodium dodecylbenzenesulfonate, 7.5 g of polyoxyethylene alkyl ether, and 190 g of ion-exchanged water were uniformly emulsified. 0.2 g of potassium persulfate was added to the separable flask, and the reaction was started by starting the dripping of the monomer emulsion. While adding the monomer emulsion to the separable flask over 4 hours, 30 g of a 3% potassium persulfate aqueous solution was added over 4 hours. After completion of addition of the monomer emulsion, it was stirred at 80° C. for 1 hour to complete the reaction. The inside of the separable flask was cooled, and 8 g of a 30% aqueous sodium hydroxid...
Embodiment 2
[0054] 150 g of ion-exchanged water was put into a 1-L five-necked detachable flask, and it heated to 80 degreeC, stirring. 46 g of methyl methacrylate, 15 g of 2-ethylhexyl acrylate, 11 g of ethyl acrylate, 18 g of acrylic acid, polyoxyethylene glycol monomethacrylate acid phosphate (manufactured by Kyoeisha Chemical Co., Ltd. 1M) 60 g, 1.5 g of sodium dodecylbenzenesulfonate, 7.5 g of polyoxyethylene alkyl ether, and 190 g of ion-exchanged water were uniformly emulsified. 0.2 g of potassium persulfate was added to the separable flask, and the reaction was started by starting the dripping of the monomer emulsion. While adding the monomer emulsion to the separable flask over 4 hours, 30 g of a 3% potassium persulfate aqueous solution was added over 4 hours. After completion of addition of the monomer emulsion, it was stirred at 80° C. for 1 hour to complete the reaction. The inside of the separable flask was cooled, and 8 g of a 30% aqueous sodium hydroxide solution was adde...
Embodiment 3
[0056] 150 g of ion-exchanged water was put into a 1-L five-necked detachable flask, and it heated to 80 degreeC, stirring. 24 g of ethyl acrylate, 34 g of methyl methacrylate, 2 g of methacrylic acid, 90 g of polyoxyethylene glycol monomethacrylic acid phosphate (manufactured by Kyoeisha Chemical Co., Ltd., Laite Extel P-1M), dodecane 1.5 g of sodium phenyl sulfonate, 7.5 g of polyoxyethylene alkyl ether, and 190 g of ion-exchanged water were uniformly emulsified. 0.2 g of potassium persulfate was added to the separable flask, and the reaction was started by starting the dripping of the monomer emulsion. While adding the monomer emulsion to the separable flask over 4 hours, 30 g of a 3% potassium persulfate aqueous solution was added over 4 hours. After completion of addition of the monomer emulsion, it was stirred at 80° C. for 1 hour to complete the reaction. The inside of the separable flask was cooled, and 8 g of a 30% aqueous sodium hydroxide solution was added to neut...
PUM
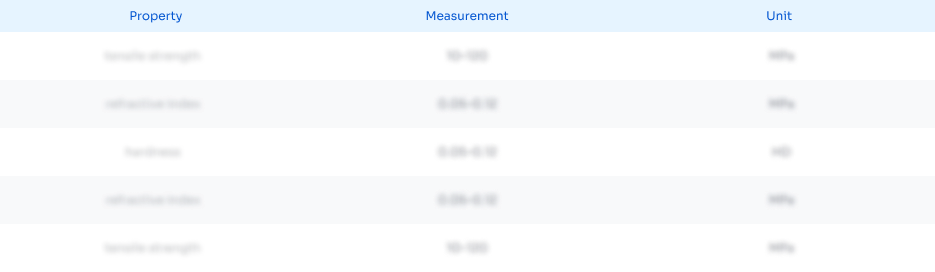
Abstract
Description
Claims
Application Information

- R&D Engineer
- R&D Manager
- IP Professional
- Industry Leading Data Capabilities
- Powerful AI technology
- Patent DNA Extraction
Browse by: Latest US Patents, China's latest patents, Technical Efficacy Thesaurus, Application Domain, Technology Topic, Popular Technical Reports.
© 2024 PatSnap. All rights reserved.Legal|Privacy policy|Modern Slavery Act Transparency Statement|Sitemap|About US| Contact US: help@patsnap.com