Method for leaching manganese from manganese-rich slag
A manganese-rich slag and leaching technology is applied in the field of manganese leaching from manganese-rich slag, which can solve the problems of difficult leaching of manganese-rich slag, affecting filtration, and difficulty in leaching of manganese-rich slag, and achieves improved leaching efficiency, strong feasibility and effect. significant effect
- Summary
- Abstract
- Description
- Claims
- Application Information
AI Technical Summary
Problems solved by technology
Method used
Image
Examples
example 1
[0041] First, mix 40 grams of manganese-rich slag (manganese content 29.11wt%, silica 27.38wt%) with 60 grams of metallurgical manganese (manganese content 21.14wt%, silica 6.69wt%), and add 30 grams of yellow iron Ore (containing FeS 2 about 70 wt%).
[0042] Next, a sulfuric acid solution with an acidity of 100 g / L was added to the above mixed powder with a liquid-solid ratio of 6:1 to obtain a slurry.
[0043] Finally, under the conditions of temperature 110° C. and pressure 0.5 MPa, leaching was carried out for 2 hours while vigorously stirring. The leached feed liquid is vacuum filtered while hot to obtain manganese leaching liquid and filter residue.
[0044] The filtrate was measured and volumetrically sent for sample analysis, and the filter residue was dried and weighed for sample analysis.
[0045] And the leaching rate measured by leachate and the leached rate measured by filter residue are calculated respectively by the following calculation formula:
[0046] L...
example 2
[0055] First, as in Example 1, 40 grams of manganese-rich slag (manganese content 29.11wt%, silicon dioxide 27.38wt%) and 60 grams of metallurgical manganese (manganese content 21.14wt%, silicon dioxide 6.69wt%) were evenly mixed , and add an appropriate amount of pyrite.
[0056] Next, add sulfuric acid with an acidity of 130 g / L to the above mixed powder with a liquid-solid ratio of 7:1 to obtain a slurry.
[0057]Finally, under the conditions of temperature 100° C. and pressure 0.3 MPa, leaching was carried out for 2 hours while vigorously stirring. The leached feed liquid is filtered under pressure while hot to obtain manganese leaching liquid and filter residue.
[0058] The filtrate was measured and volumetrically sent for sample analysis, and the filter residue was dried and weighed for sample analysis.
[0059] Similarly, the leaching rate was calculated by the above calculation method, and the results showed that the leaching rate was 93.6% in terms of leachate and ...
PUM
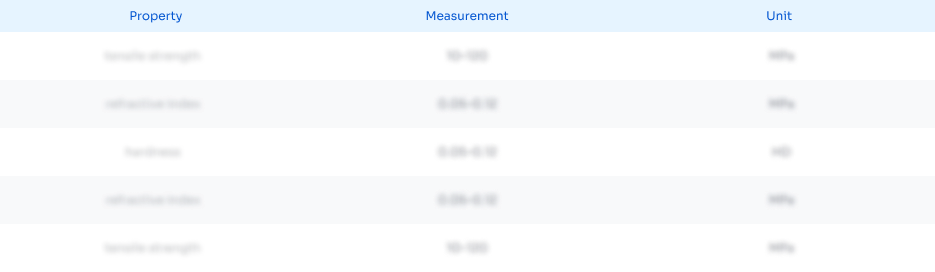
Abstract
Description
Claims
Application Information

- Generate Ideas
- Intellectual Property
- Life Sciences
- Materials
- Tech Scout
- Unparalleled Data Quality
- Higher Quality Content
- 60% Fewer Hallucinations
Browse by: Latest US Patents, China's latest patents, Technical Efficacy Thesaurus, Application Domain, Technology Topic, Popular Technical Reports.
© 2025 PatSnap. All rights reserved.Legal|Privacy policy|Modern Slavery Act Transparency Statement|Sitemap|About US| Contact US: help@patsnap.com