Process for recovering silver, lead and bismuth from silver-bearing soot comprehensively
A soot and form technology, applied in the process of lead and bismuth, in the field of comprehensive recovery of silver, can solve the problems of low direct silver yield, environmental pollution by flue gas, short process flow, etc., and achieve rapid capital turnover, high recovery rate, and technological Environmentally friendly process
- Summary
- Abstract
- Description
- Claims
- Application Information
AI Technical Summary
Problems solved by technology
Method used
Image
Examples
experiment approach 1
[0026] (1) Take 500g of silver-containing soot (0.8%-5% silver, 40%-50% lead, 5-10% bismuth, 10%-20% zinc) and heat it with 2L water at 85-95°C and stir for 2-3 hours After filtering, the filtrate is reused; the filter residue (dechlorinated mud) is heated with 250g of sulfuric acid, 35kg of water, and 5g of hydrogen peroxide, and the temperature is controlled at 85-95°C. After stirring for 2-3 hours, the pH of the end point is controlled to be 2.5-3.5, and then filtered;
[0027] (2) Filtrate to obtain 385g of filter residue and 17500mL of filtrate; the filter residue contains 52.1% lead and 10.9% bismuth; add reduced coal and soda ash to the filter residue and melt it in a reverberatory furnace to obtain lead-bismuth alloy. After electrolysis of lead-bismuth alloy Precipitated lead and bismuth-containing anode slime (bismuth-containing greater than 95%) are obtained; bismuth-containing anode slime is fed into the bismuth refining pot in sequence, and then 99.99% of refined bi...
experiment approach 2
[0031] (1) Take 10kg of silver-containing soot (containing 1.36% of silver, 40.1% of lead, 6.9% of bismuth, and 23.4% of zinc) and heat it with 40L of water, stir and wash it for 3 hours, then filter it, and reuse the filtrate; use 5kg of sulfuric acid for the filter residue (dechlorinated mud) , 35kg of water, 500g of hydrogen peroxide, heated (temperature 90°C) and stirred for 3 hours, then filtered;
[0032] (2) Filter to obtain 7.48kg of filter residue and 39000L of filtrate; the filter residue contains 53.2% lead and 9.1% bismuth; add reduced coal and soda ash to the filter residue and enter the reverberatory furnace for smelting to obtain lead-bismuth alloy, lead-bismuth alloy electrolysis Finally, the precipitated lead and bismuth-containing anode slime (bismuth-containing greater than 95%) are obtained; the bismuth-containing anode slime is fed into the bismuth refining pot in sequence, and then 99.99% of refined bismuth can be produced;
[0033] (3) After adding 90g o...
experiment approach 3
[0036] (1) Take 500g of silver-containing soot (containing 1.51% of silver, 40.6% of lead, 8.5% of bismuth, and 20.2% of zinc) with 2L of clean water, heating, stirring and cleaning for 3 hours, then filtering, and reusing the filtrate; filter residue (dechlorinated mud) with 250g of sulfuric acid , 35kg of water, 5g of hydrogen peroxide, heated (temperature 90°C) and stirred for 3 hours, then filtered;
[0037] (2) Filtrate to obtain 385g of filter residue and 17500mL of filtrate; the filter residue contains 52.1% lead and 10.9% bismuth; add reduced coal and soda ash to the filter residue and melt it in a reverberatory furnace to obtain lead-bismuth alloy. After electrolysis of lead-bismuth alloy Precipitated lead and bismuth-containing anode slime (bismuth-containing greater than 95%) are obtained; bismuth-containing anode slime is fed into the bismuth refining pot in sequence, and then 99.99% of refined bismuth can be produced after successively feeding oxygen, zinc ingots, ...
PUM
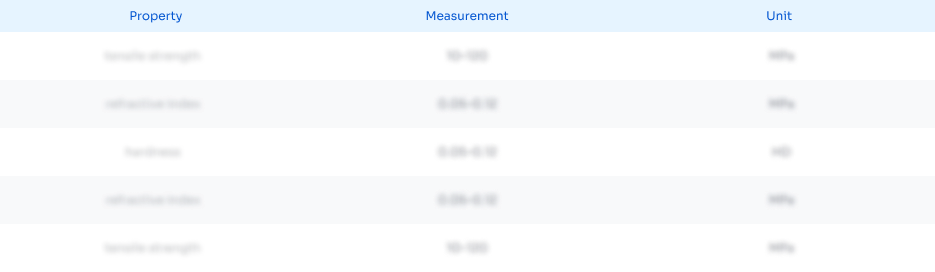
Abstract
Description
Claims
Application Information

- R&D
- Intellectual Property
- Life Sciences
- Materials
- Tech Scout
- Unparalleled Data Quality
- Higher Quality Content
- 60% Fewer Hallucinations
Browse by: Latest US Patents, China's latest patents, Technical Efficacy Thesaurus, Application Domain, Technology Topic, Popular Technical Reports.
© 2025 PatSnap. All rights reserved.Legal|Privacy policy|Modern Slavery Act Transparency Statement|Sitemap|About US| Contact US: help@patsnap.com