Ethylene-propylene-diene rubber compound and its preparation method
A technology of EPDM and EPDM, applied in the field of rubber materials, can solve the problems of high production cost, low production efficiency, high cost of molding die, etc., and achieve the effects of excellent ozone resistance and improved production efficiency.
- Summary
- Abstract
- Description
- Claims
- Application Information
AI Technical Summary
Problems solved by technology
Method used
Examples
Embodiment 1
[0039] (1) The ingredients of each component are weighed according to the weight ratio:
[0040] Main ingredients: 30% EPDM raw rubber;
[0041] Accessories: Reinforcing agent is 36% carbon black with low structure and fast pressing;
[0042] Softener is 15% paraffin oil;
[0043] Hygroscopic agent is 3.1% calcium oxide;
[0044] The filler is light calcium carbonate 10%;
[0045] Additives: The accelerator is 0.2% zinc dibutyl dithiocarbamate, 0.1% zinc dimethyl dithiocarbamate, 0.2% dibenzothiazole disulfide and N-cyclohexyl-2-benzothiazolyl Sulfonamide 0.40% mixed;
[0046] The active agent is zinc oxide and stearic acid mixed in a mass ratio of 5:2, totaling 1.7%;
[0047] Functional additives are high styrene resin 7%;
[0048] The vulcanizing agent is 0.4% sulfur;
[0049] The modifier is 0.9% polyethylene glycol, and the total composition is 100%;
[0050] (2) Plasticizing the functional additives on the open mill;
[0051] (3) Put the EPDM rubber, plasticized functional additives, rei...
Embodiment 2
[0058] (1) The raw materials of each component are weighed according to the weight ratio:
[0059] Main ingredients: 30% EPDM raw rubber;
[0060] Accessories: Reinforcing agent is 36% carbon black with low structure and fast pressing;
[0061] Softener is 15% paraffin oil;
[0062] Hygroscopic agent is 3.1% calcium oxide;
[0063] The filler is light calcium carbonate 0;
[0064] Additives: accelerator zinc dibutyl dithiocarbamate 0.35%, dithiol benzothiazole 0.15%, dibenzothiazole disulfide 0.3%, and N-cyclohexyl-2-benzothiazolyl sulfenamide 0.5% mixed;
[0065] The active agent is 2.5% of zinc oxide and stearic acid in a mass ratio of 2:1;
[0066] Functional additives are high styrene resin 10%;
[0067] The vulcanizing agent is sulfur 0.5%;
[0068] The modifier is polyethylene glycol 1.6%, and the total composition is 100%;
[0069] (2) Plasticizing the functional additives on the open mill;
[0070] (3) Put the EPDM rubber, plasticized functional additives, reinforcing agents, fillers,...
Embodiment 3
[0077] (1) The raw materials of each component are weighed according to the weight ratio:
[0078] Main ingredient: 27% EPDM raw rubber;
[0079] Accessories: Reinforcing agent is 40% carbon black with low structure and fast pressing;
[0080] Softener is 17% paraffin oil;
[0081] Hygroscopic agent is 3.4% calcium oxide;
[0082] The filler is light calcium carbonate 0;
[0083] Additives: accelerator dithiol benzothiazole 0.3%, zinc dimethyl dithiocarbamate 0.3%, dibenzothiazole disulfide 0.2%, or N-cyclohexyl-2-benzothiazolyl sulfenamide 0.4% mixed;
[0084] The active agent is zinc oxide and stearic acid with a mass ratio of 5:1 totaling 1.7%;
[0085] Functional additives are 8.1% high styrene resin;
[0086] The vulcanizing agent is 0.4% sulfur;
[0087] The modifier is polyethylene glycol 1.4%, and the total composition is 100%;
[0088] (2) Plasticizing the functional additives on the open mill;
[0089] (3) Put the EPDM rubber, plasticized functional additives, reinforcing agents, fi...
PUM
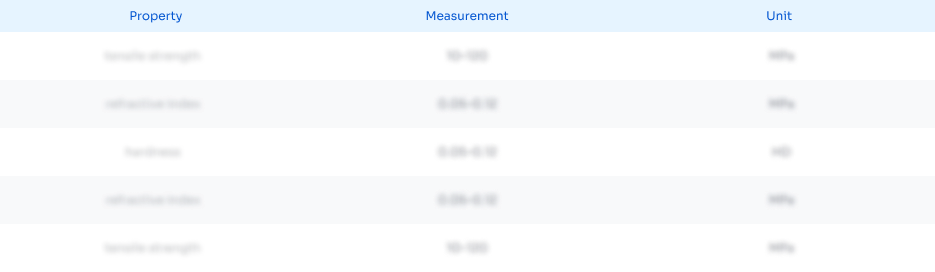
Abstract
Description
Claims
Application Information

- Generate Ideas
- Intellectual Property
- Life Sciences
- Materials
- Tech Scout
- Unparalleled Data Quality
- Higher Quality Content
- 60% Fewer Hallucinations
Browse by: Latest US Patents, China's latest patents, Technical Efficacy Thesaurus, Application Domain, Technology Topic, Popular Technical Reports.
© 2025 PatSnap. All rights reserved.Legal|Privacy policy|Modern Slavery Act Transparency Statement|Sitemap|About US| Contact US: help@patsnap.com