Methods of forming photolithographic patterns
A lithography patterning and patterning technology, applied in the field of lithography process, can solve the problems of small exposure latitude, small processing window, explosion, etc.
- Summary
- Abstract
- Description
- Claims
- Application Information
AI Technical Summary
Problems solved by technology
Method used
Image
Examples
Embodiment 1
[0055] The procedure in Comparative Example 1 was repeated except that 5-methyl-2-hexanone was used instead of n-butyl acetate as the developer. Provides a 60nm (measured 61.25nm) target CD exposure is 39.40mJ / cm 2 . In this case, the precise pattern of the contact hole has a uniform size and final shape. The resulting exposure latitude is 15% and the CD uniformity (3σ) is 7.22.
Embodiment 2
[0057] The procedure in Comparative Example 1 was repeated except that 2-heptanone was used instead of n-butyl acetate as the developer. Visual inspection after development showed no residue on the wafer surface. Provides a 60nm (measured 60.73nm) target CD exposure is 51.10mJ / cm 2 . In this case, the precise pattern of the contact hole has a uniform size and final shape. The resulting exposure latitude is 32% and the CD uniformity (3σ) is 7.07.
[0058] Table 1
[0059] Comparison
[0060] *Safety standards advocated by the National Fire Protection Association (U.S.). Each item of health, flammability and reaction is evaluated from 0 (no danger; ordinary substance) to 4 (severe danger).
PUM
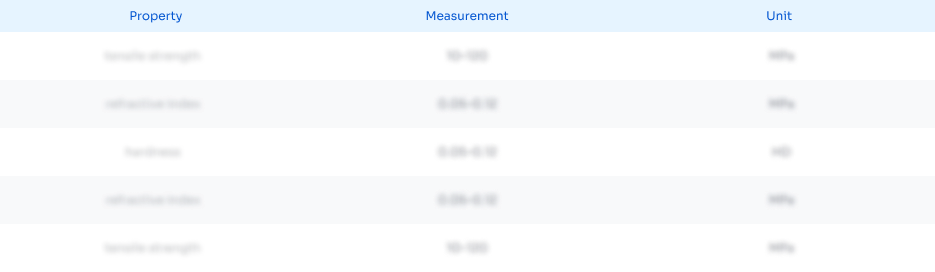
Abstract
Description
Claims
Application Information

- R&D
- Intellectual Property
- Life Sciences
- Materials
- Tech Scout
- Unparalleled Data Quality
- Higher Quality Content
- 60% Fewer Hallucinations
Browse by: Latest US Patents, China's latest patents, Technical Efficacy Thesaurus, Application Domain, Technology Topic, Popular Technical Reports.
© 2025 PatSnap. All rights reserved.Legal|Privacy policy|Modern Slavery Act Transparency Statement|Sitemap|About US| Contact US: help@patsnap.com