Vertical air extraction preparation process of vacuum glass
A technology of vacuum glass and preparation process, which is applied in glass manufacturing equipment, glass forming, glass reshaping, etc. It can solve the problems of affecting the quality of vacuum glass, insufficient vacuum degree, and difficulty in taking over pipes, so as to realize continuous production and improve Vacuum degree, simple and easy operation
- Summary
- Abstract
- Description
- Claims
- Application Information
AI Technical Summary
Problems solved by technology
Method used
Image
Examples
Embodiment Construction
[0023] The present invention will be further described in detail below in conjunction with the accompanying drawings and through specific embodiments. The following embodiments are only descriptive, not restrictive, and cannot limit the protection scope of the present invention.
[0024] In order to clearly describe the embodiment of the present invention, the manufacturing system of the present invention will be described first.
[0025] see figure 1 , 2 3. The manufacturing system includes a high-temperature heating box and a low-temperature pumping box. The high-temperature heating box is composed of a movable sealing box cover 10 and a heating box 11. The moving sealing box cover is a door-type structure, and the sealing cover is installed on the heating box. Both the box cover and the heating box are equipped with thermal insulation materials, and a mobile bracket 12 is installed on both sides of the mobile sealing box cover. The lower end of the mobile bracket is equipp...
PUM
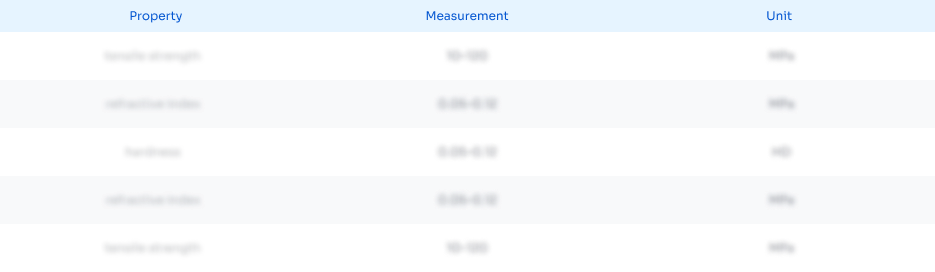
Abstract
Description
Claims
Application Information

- R&D
- Intellectual Property
- Life Sciences
- Materials
- Tech Scout
- Unparalleled Data Quality
- Higher Quality Content
- 60% Fewer Hallucinations
Browse by: Latest US Patents, China's latest patents, Technical Efficacy Thesaurus, Application Domain, Technology Topic, Popular Technical Reports.
© 2025 PatSnap. All rights reserved.Legal|Privacy policy|Modern Slavery Act Transparency Statement|Sitemap|About US| Contact US: help@patsnap.com