High glowing filament flame-retardant PA (polyamide)/PPO (polyphenyleneoxide) alloy and preparation method thereof
A high-glow wire and alloy technology, applied in the field of polymer materials, can solve the problems that cannot meet the requirements of glow wire
- Summary
- Abstract
- Description
- Claims
- Application Information
AI Technical Summary
Problems solved by technology
Method used
Image
Examples
Embodiment 1
[0035] PA6 51.5% (weight percentage, the same below), PPO 15%, flame retardant 18%, flame retardant synergist 6%, compatibilizer 5%, toughening agent 4%, antioxidant 1010 / 168 0.2 / 0.2 %, other additives 0.1%.
[0036] Preparation method: first dry PA6, PPO and toughening agent in a vacuum drying oven at 80°C for 4 to 8 hours, weigh the dried PA6, PPO resin and various additives according to the proportion, and put all the raw materials into the The feeding hopper of the twin-screw extruder is melt-extruded and granulated; the processing technology is as follows: the temperature of the first zone of the twin-screw extruder is 140-180°C, the temperature of the second zone is 190-220°C, and the temperature of the third zone is 220-230°C. The temperature in the fourth zone is 230-250°C, the head is 180-220°C, the residence time is 2-3min, the pressure is 12-18MPa, and the screw speed is 130-150 rpm.
Embodiment 2
[0038] PA6 58.5% (weight percentage, the same below), PPO 10%, flame retardant 18%, flame retardant synergist 6, compatibilizer 4%, toughening agent 3%, antioxidant 1010 / 168 0.2 / 0.2% , Other additives 0.1%.
[0039] Preparation method: first dry PA6, PPO and toughening agent in a vacuum drying oven at 80°C for 4 to 8 hours, weigh the dried PA6, PPO resin and various additives according to the proportion, and put all the raw materials into the The feeding hopper of the twin-screw extruder is melt-extruded and granulated; the processing technology is as follows: the temperature of the first zone of the twin-screw extruder is 140-180°C, the temperature of the second zone is 190-220°C, and the temperature of the third zone is 220-230°C. The temperature in the fourth zone is 230-250°C, the head is 180-220°C, the residence time is 2-3min, the pressure is 12-18MPa, and the screw speed is 130-150 rpm.
Embodiment 3
[0041] PA6 63.6% (weight percentage, the same below), PPO 8%, flame retardant 18.5%, flame retardant synergist 6.2, compatibilizer 4%, toughening agent 3%, antioxidant 1010 / 168 0.2 / 0.2% , Other additives 0.3%.
[0042] Preparation method: first dry PA6, PPO and toughening agent in a vacuum drying oven at 80°C for 4 to 8 hours, weigh the dried PA6, PPO resin and various additives according to the proportion, and put all the raw materials into the The feeding hopper of the twin-screw extruder is melt-extruded and granulated; the processing technology is as follows: the temperature of the first zone of the twin-screw extruder is 140-180°C, the temperature of the second zone is 190-220°C, and the temperature of the third zone is 220-230°C. The temperature in the fourth zone is 230-250°C, the head is 180-220°C, the residence time is 2-3min, the pressure is 12-18MPa, and the screw speed is 130-150 rpm.
PUM
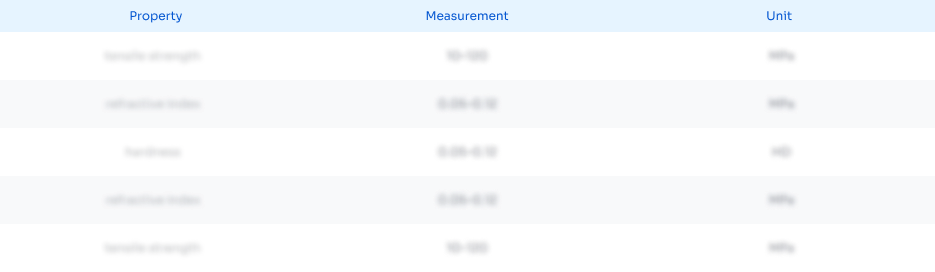
Abstract
Description
Claims
Application Information

- Generate Ideas
- Intellectual Property
- Life Sciences
- Materials
- Tech Scout
- Unparalleled Data Quality
- Higher Quality Content
- 60% Fewer Hallucinations
Browse by: Latest US Patents, China's latest patents, Technical Efficacy Thesaurus, Application Domain, Technology Topic, Popular Technical Reports.
© 2025 PatSnap. All rights reserved.Legal|Privacy policy|Modern Slavery Act Transparency Statement|Sitemap|About US| Contact US: help@patsnap.com