A kind of sintering mold of thyristor chip and molybdenum sheet and using method thereof
A technology of silicon chips and molds, applied in electrical components, semiconductor/solid-state device manufacturing, circuits, etc., can solve the dislocation of silicon chips and molybdenum chips, the influence of product flow capacity and appearance, and the sintering process of molybdenum chips and silicon chips Not too standardized and other issues, to achieve the effect of improving production efficiency and good heat transfer
- Summary
- Abstract
- Description
- Claims
- Application Information
AI Technical Summary
Problems solved by technology
Method used
Image
Examples
Embodiment Construction
[0028] Such as figure 1 and 2 As shown, a sintering mold of a thyristor chip and a molybdenum sheet of the present invention comprises a sintering mold body 1, and a plurality of holes 2 that are convenient for vertical exhaust are arranged in the middle of the sintering mold body 1, so as to facilitate vertical exhaust. Below the hole 2, there is a hole 3 for horizontal exhaust, and the top of the hole 2 for vertical exhaust is provided with an upper positioning step 4, a middle positioning step 5 and a lower positioning step 6 from top to bottom, and the sintering mold body 1 is surrounded. There are steps 7 for stacking, the diameter of the lower positioning step 6<the diameter of the middle positioning step 5<the diameter of the upper positioning step 4.
[0029] The mold material adopts electronic graphite, which can ensure good heat transfer during the sintering process and can make the three-layer parts of the product be positioned reliably; the thermal conductivity is...
PUM
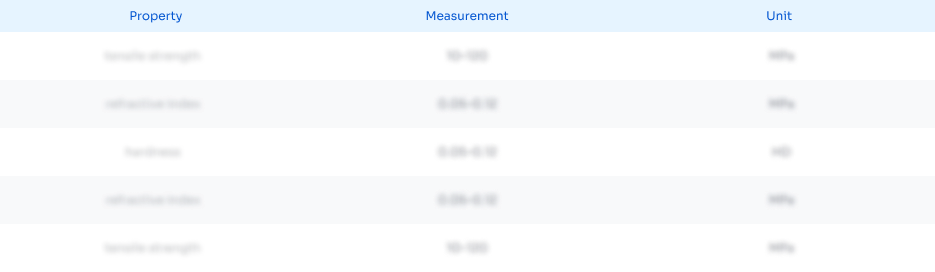
Abstract
Description
Claims
Application Information

- R&D Engineer
- R&D Manager
- IP Professional
- Industry Leading Data Capabilities
- Powerful AI technology
- Patent DNA Extraction
Browse by: Latest US Patents, China's latest patents, Technical Efficacy Thesaurus, Application Domain, Technology Topic, Popular Technical Reports.
© 2024 PatSnap. All rights reserved.Legal|Privacy policy|Modern Slavery Act Transparency Statement|Sitemap|About US| Contact US: help@patsnap.com