High-strength reinforcement built-in ultra high performance concrete (UHPC) beam member
A technology of ultra-high-performance and high-strength steel bars, which is applied in the direction of building components, building reinforcements, joists, etc., can solve the problems of difficult construction, insufficient compressive strength, and high construction costs, so as to reduce the consumption of raw materials and energy, The effect of increasing the available space and reducing the difficulty of construction
- Summary
- Abstract
- Description
- Claims
- Application Information
AI Technical Summary
Problems solved by technology
Method used
Image
Examples
Embodiment 1
[0028] This embodiment corresponds to figure 1 The solid rectangle shown and figure 2 For the hollow rectangular section shown, first make the outer formwork according to the size of the section. figure 2 The hollow section shown still needs to make an inner formwork, the outer formwork adopts steel formwork or wood formwork, and the inner formwork adopts the same material as the outer formwork. When the inner formwork is circular, an inflatable rubber bag can also be used.
[0029] Secondly, the reinforcing bar skeleton is bound, and the reinforcing bar skeleton is made up of tensile reinforcing bar 1, stirrup 3 and longitudinal compression reinforcing bar 4, and longitudinal tensile reinforcing bar 1 and longitudinal compression reinforcing bar 4 are attached to the inner side of stirrup 3 and bound together with it; Longitudinal tension reinforcement 1 adopts high-strength reinforcement, stirrup 3 and longitudinal compression reinforcement 4 can adopt high-strength reinf...
Embodiment 2
[0032] This embodiment corresponds to image 3 For the T-shaped section shown, first make the outer formwork according to the size of the section, and the outer formwork is made of steel formwork.
[0033] Secondly, the reinforcement skeleton is bound. The reinforcement skeleton is composed of tension reinforcement 1, stirrup 3, longitudinal compression reinforcement 4, distribution reinforcement 5 and roof stress reinforcement 6. The longitudinal tension reinforcement 1 is attached to the inner side of the stirrup 3 and connected with it. Binding together, the distribution reinforcement 5 is attached to the outer side of the stirrup 3 and bound together; the longitudinal compression reinforcement 4 is attached to the inner side of the roof stress reinforcement 6, and the roof stress reinforcement 6 is connected to the stirrup 3 to form an effective connection; Among them, the longitudinal tensile reinforcement 1 and the roof stress reinforcement 6 are high-strength reinforcem...
Embodiment 3
[0036] This embodiment corresponds to Figure 4 For the box section shown, the formwork is first made according to the size of the section, and the inner and outer formworks are all made of steel formwork.
[0037] Secondly, the reinforcement skeleton is bound, and the reinforcement skeleton is composed of tensile reinforcement 1, stirrup 3, longitudinal compression reinforcement 4, distribution reinforcement 5 and roof stress reinforcement 6. Among them, the stirrup 3 forms a closed double layer, the longitudinal tensile steel bar 1 is attached to the inner side of the stirrup 3 and bound together with it, and the distribution steel bar 5 is arranged on the inner and outer sides of the box girder web at the same time and attached to the inner side of the stirrup 3 The outer side is bound together with it; the longitudinal compression steel bar 4 is attached to the inner side of the top plate stress steel bar 6, and the roof stress steel bar 6 is connected with the stirrup 3 t...
PUM
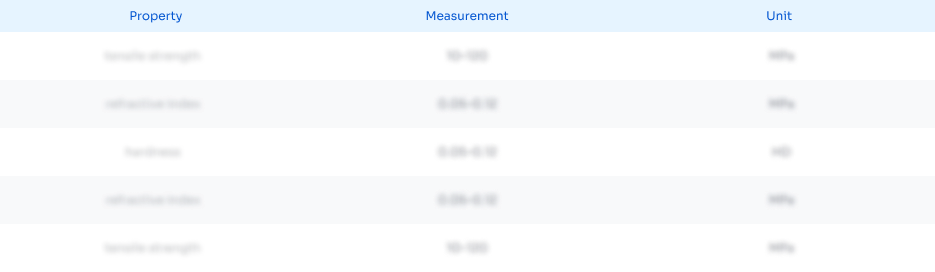
Abstract
Description
Claims
Application Information

- R&D
- Intellectual Property
- Life Sciences
- Materials
- Tech Scout
- Unparalleled Data Quality
- Higher Quality Content
- 60% Fewer Hallucinations
Browse by: Latest US Patents, China's latest patents, Technical Efficacy Thesaurus, Application Domain, Technology Topic, Popular Technical Reports.
© 2025 PatSnap. All rights reserved.Legal|Privacy policy|Modern Slavery Act Transparency Statement|Sitemap|About US| Contact US: help@patsnap.com