Acrylic polyurethane hot-dip galvanized substrate coating and preparation method thereof
An acrylic polyurethane and substrate coating technology, applied in the coating field, can solve the problems of poor adhesion, poor resistance to humidity and heat, affecting the construction of the next paint, difficult adhesion, etc., and achieves good film compactness and excellent resistance to boiling water. The effect of cookability and excellent adhesion strength
- Summary
- Abstract
- Description
- Claims
- Application Information
AI Technical Summary
Problems solved by technology
Method used
Image
Examples
example 1
[0027] An acrylic primer for mica iron hot dip galvanizing.
[0028] Group A distribution table:
[0029] Table 1 Distribution ratio of group A
[0030]
[0031] like figure 1 The preparation method of shown A component comprises the following steps:
[0032] Firstly, put anhydrous butyl acetate (above 99.9%), low molecular weight polyol polymer TP, trimethylolpropane (TMP) and 1 / 2 phosphoric acid into the reaction kettle, stir and heat up. When the temperature rises to 60-65°C and TMP is completely dissolved, put in MDI and TDI, keep the temperature at 70-75°C for 4-5 hours, take samples to measure the NCO% content and free TDI% content, and put in the solvent anhydrous xylene after reaching the standard , cooled to below 50°C, filtered, packaged, and sealed for storage.
[0033] Group B distribution table:
[0034] Table 2 Distribution ratio of group B
[0035]
[0036] Above-mentioned preparation method comprises the following steps: Resin and additives are m...
example 2
[0039] A light gray acrylic polyurethane hot-dip galvanized substrate all-in-one coating
[0040] The distribution ratio and preparation method of group A are the same as in Example 1.
[0041] The allocation ratio of group B is shown in Table 3.
[0042] Table 3 Proportion of a light gray acrylic polyurethane hot-dip galvanized substrate bottom-surface-integrated coating
[0043]
[0044] like figure 2 The preparation method shown includes the following steps: Resin and additives are mixed and dissolved: (1) Add epoxy-modified hydroxyacrylic resin, fumed silica, hyperdispersant, mixed solvent of xylene, butyl acetate, and ethyl lactate in sequence. Start the mixer, and stir at medium and low speed (500~800r / min) for about 20~30 minutes to fully dissolve and mix. High speed pre-dispersion : (2) Add titanium dioxide, iron red powder, high-pigment carbon black and phthalocyanine blue sequentially while dispersing at medium speed (500~800r / min) in (1). Continue to dis...
PUM
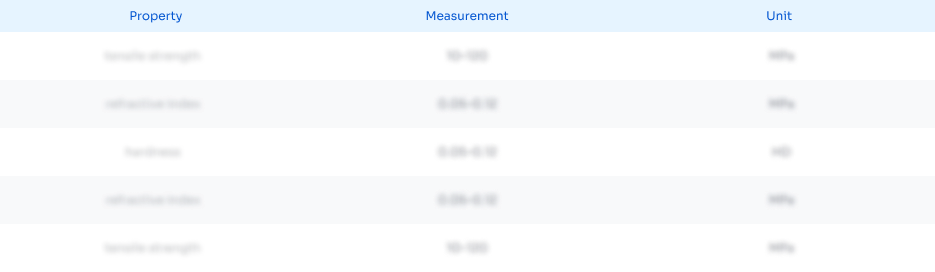
Abstract
Description
Claims
Application Information

- R&D
- Intellectual Property
- Life Sciences
- Materials
- Tech Scout
- Unparalleled Data Quality
- Higher Quality Content
- 60% Fewer Hallucinations
Browse by: Latest US Patents, China's latest patents, Technical Efficacy Thesaurus, Application Domain, Technology Topic, Popular Technical Reports.
© 2025 PatSnap. All rights reserved.Legal|Privacy policy|Modern Slavery Act Transparency Statement|Sitemap|About US| Contact US: help@patsnap.com