A kind of preparation method of oxide dispersion strengthened nickel base alloy
A nickel-based alloy and dispersion-strengthening technology, which is applied in the field of oxide dispersion-strengthening nickel-based alloy preparation, can solve the problems of complex process, difficult oxides, expensive equipment, etc., and achieve the effect of simple process and good technical effect.
- Summary
- Abstract
- Description
- Claims
- Application Information
AI Technical Summary
Problems solved by technology
Method used
Image
Examples
Embodiment 1
[0026] Example 1 A preparation method of oxide dispersion strengthened nickel-based alloy
[0027] First adopt mechanical ball milling mode to carry out uniform mixing to micron level nickel powder (mass ratio 9.5%), diyttrium trioxide powder (mass ratio 5%), tungsten powder (mass ratio 85.5%); Mixing medium adopts acetone, ball milling time is 20 Hours; then molded by compression molding, the green body is sintered after molding; the sintering furnace adopts a continuous atmosphere protection tube furnace, the atmosphere uses high-purity hydrogen, and the flow rate is controlled at 30-40ml / min.cm 2 ; The isothermal sintering temperature is 1500°C, and the holding time is 0.5 hours; after the isothermal sintering is completed, cool to room temperature with the furnace and take it out. The obtained master alloy microstructure is shown in figure 1 .
[0028] Melt the master alloy (accounting for 5% of the total alloy mass) and the K418 master alloy in a vacuum induction furnac...
Embodiment 2
[0029] Example 2 A preparation method of oxide dispersion strengthened nickel-based alloy
[0030] First adopt mechanical ball milling mode to carry out uniform mixing to nano-micron level nickel powder (mass ratio 10%), diyttrium trioxide powder (mass ratio 10%), tungsten powder (mass ratio 80%); Mixing medium adopts acetone, ball milling time is 15 hours; then molded by compression molding, and the green body is sintered after molding; the sintering furnace adopts a continuous atmosphere protection tube furnace, the atmosphere uses high-purity hydrogen, and the flow rate is controlled at 30-40ml / min.cm 2 ; The isothermal sintering temperature is 1400°C, and the holding time is 2 hours; after the isothermal sintering is completed, cool to room temperature with the furnace and take it out.
[0031] Melt the master alloy (accounting for 10% of the total mass of the alloy) and the K417 master alloy in a vacuum induction furnace. After the alloy is completely melted, increase the...
Embodiment 3
[0032] Example 3 A preparation method of oxide dispersion strengthened nickel-based alloy
[0033] Firstly, the micron-level nickel powder (95% by mass) and yttrium trioxide powder (5% by mass) are uniformly mixed by mechanical ball milling; the mixing medium is n-ethane, and the ball milling time is 30 hours; Carry out molding, and sinter the biscuit after molding; the sintering furnace adopts a continuous atmosphere protection tube furnace, and uses a mixed gas of high-purity hydrogen and high-purity nitrogen. The ratio of hydrogen to nitrogen is between 1:1, and the reducing gas The flow can be controlled at 20-30ml / min.cm 2 ; The isothermal sintering temperature is 1400°C, and the holding time is 2 hours;
[0034] Melt the master alloy (accounting for 8% of the total alloy mass) and the K452 master alloy in a vacuum induction furnace. After the alloy is completely melted, increase the power to electromagnetically stir the alloy liquid for 3-5 minutes, and then reduce the ...
PUM
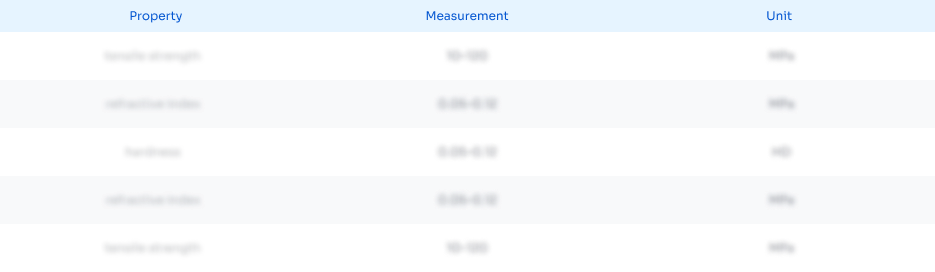
Abstract
Description
Claims
Application Information

- R&D
- Intellectual Property
- Life Sciences
- Materials
- Tech Scout
- Unparalleled Data Quality
- Higher Quality Content
- 60% Fewer Hallucinations
Browse by: Latest US Patents, China's latest patents, Technical Efficacy Thesaurus, Application Domain, Technology Topic, Popular Technical Reports.
© 2025 PatSnap. All rights reserved.Legal|Privacy policy|Modern Slavery Act Transparency Statement|Sitemap|About US| Contact US: help@patsnap.com