Processing method of monolithic sintered superhard abrasive honing tool sleeve
A superhard abrasive and processing method technology, applied in honing tools, metal processing equipment, manufacturing tools, etc., can solve the problems of affecting the service life of the tool holder, easy falling off of diamond grinding discs, inconsistent changes in the tool body, etc., to improve the service life , The internal structure is uniform and dense, and the effect of reducing the cutting load
- Summary
- Abstract
- Description
- Claims
- Application Information
AI Technical Summary
Problems solved by technology
Method used
Image
Examples
Embodiment 1
[0028] Evenly distribute the copper powder in the mold, and evenly mix the powdered diamond and metal binder into the middle part of the cutter body, stir evenly, so that the diamond is evenly mixed into the binder, and press through the mold to form a hollow cylindrical molded part 1; In weight percentage, the total amount of copper powder and metal binder is 40%; diamond is 60%; in weight, the ratio of copper powder and metal binder is 3: 1; The guide part 11 is processed by copper powder, and the middle part 12 of the molded part 1, that is, the cutting part of the cutter sleeve, is processed by a mixture of copper powder and diamond. The molded part 1 is sintered at a temperature of 700° and the sintering time is 2 hours, keep warm for 2 hours, and then cool naturally in the air; the sintered molded part 1 is grooved by a special electric spark machine to form a chip removal groove 2. The flute 2 can be a straight groove or a spiral groove. In order to facilitate the use o...
Embodiment 2
[0031] Evenly distribute the copper powder in the mold, and evenly mix the powdered diamond and metal binder into the middle part of the cutter body, stir evenly, so that the diamond is evenly mixed into the binder, and press through the mold to form a hollow cylindrical molded part 1; In weight percentage, the total amount of copper powder and metal bond is 60%; diamond is 40%; in weight, the ratio of copper powder and metal bond is 3:1; The guide part 11 is processed by copper powder, and the middle part 12 of the molded part 1, namely the cutting part of the cutter sleeve, is processed by a mixture of copper powder and diamond. The molded part 1 is sintered at a temperature of 750°C and the sintering time is 2.5 hours, keep warm for 2 hours, and then cool naturally in the air; the sintered molded part 1 is grooved by a special electric spark machine to form a chip removal groove 2. The flute 2 can be a straight groove or a spiral groove. In order to facilitate the use of th...
Embodiment 3
[0034] The copper powder is evenly distributed in the mold, and the middle part of the cutter body is evenly mixed with powdery diamond and metal binder, and stirred evenly, so that the diamond is evenly mixed into the binder, and pressed into a hollow cylinder by combination or high-pressure mold Formed part 1; in weight percentage, the total amount of copper powder and metal binder is 80%; diamond is 20%; in weight, the ratio of copper powder and metal binder is 3: 1; two parts of molded part 1 The end, that is, the guide part 11 of the knife sleeve is processed by copper powder, and the middle part 12 of the formed part 1, that is, the cutting part of the knife sleeve, is processed by a mixture of copper powder and diamond. The formed part 1 is sintered at a temperature of 800 ℃, the sintering time is 2 hours, the heat preservation is 2 hours, and then naturally cooled in the air; the sintered molded part 1 is grooved by a special electric spark machine to form a chip remova...
PUM
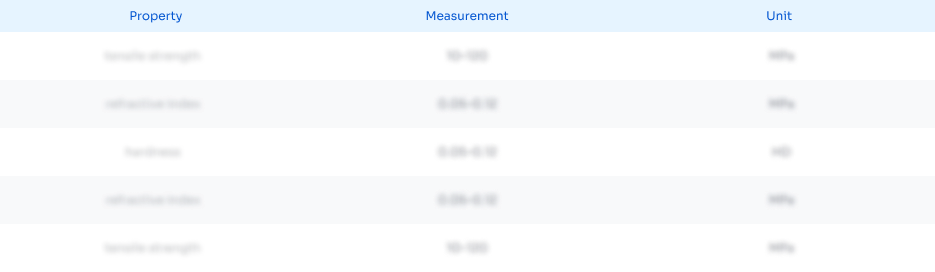
Abstract
Description
Claims
Application Information

- R&D Engineer
- R&D Manager
- IP Professional
- Industry Leading Data Capabilities
- Powerful AI technology
- Patent DNA Extraction
Browse by: Latest US Patents, China's latest patents, Technical Efficacy Thesaurus, Application Domain, Technology Topic, Popular Technical Reports.
© 2024 PatSnap. All rights reserved.Legal|Privacy policy|Modern Slavery Act Transparency Statement|Sitemap|About US| Contact US: help@patsnap.com