Process and device for recycling flue gas afterheat of electric furnace
A flue gas waste heat and electric furnace technology, which is applied in the field of iron and steel metallurgy, can solve the problems of fast cooling speed, slow recovery of waste heat, large cooling water volume, etc., and achieve the effects of avoiding recombination, achieving standard discharge, and high heat exchange intensity
- Summary
- Abstract
- Description
- Claims
- Application Information
AI Technical Summary
Problems solved by technology
Method used
Image
Examples
Embodiment Construction
[0010] The embodiments of the present invention will be further described in detail below in conjunction with the accompanying drawings: a process for recovering and utilizing waste heat from electric furnace flue gas: figure 1 Shown: the high-temperature flue gas that electric furnace 6 produces, first passes fume cover 7, vaporization cooling flue 10, enters combustion settling chamber 4, and the harmful substances such as combustible gas and dioxin in the flue gas are fully burned and decomposed here. The flue gas with a temperature of 850-1000°C coming out of the combustion settling chamber 4 enters the regenerative rapid cooling device 11, which is composed of two sets of heat exchange units A8 and B9. After the heat is transferred to the circulating air, the temperature drops below 150°C, and then the flue gas enters the high-efficiency bag filter 16 for fine dust removal, ensuring that the dust content of the flue gas coming out of the high-efficiency bag filter 16 is re...
PUM
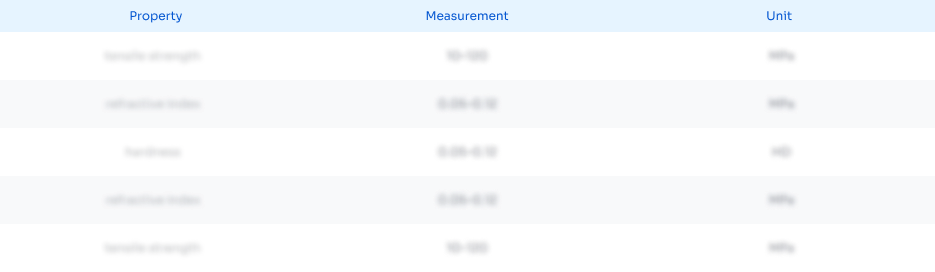
Abstract
Description
Claims
Application Information

- R&D Engineer
- R&D Manager
- IP Professional
- Industry Leading Data Capabilities
- Powerful AI technology
- Patent DNA Extraction
Browse by: Latest US Patents, China's latest patents, Technical Efficacy Thesaurus, Application Domain, Technology Topic, Popular Technical Reports.
© 2024 PatSnap. All rights reserved.Legal|Privacy policy|Modern Slavery Act Transparency Statement|Sitemap|About US| Contact US: help@patsnap.com