Polyolefin film and preparation method thereof
A film preparation and polyolefin technology, applied in electrical components, circuits, battery pack components, etc., can solve the problems of large aperture, battery short circuit, and reduced adaptability of different raw materials, etc., to achieve the effect of small structure and large quantity
- Summary
- Abstract
- Description
- Claims
- Application Information
AI Technical Summary
Problems solved by technology
Method used
Image
Examples
preparation example Construction
[0029] The preparation method of polyolefin film of the present invention is that polyolefin resin and low molecular weight compound (pore forming agent) (one of them Isopar E oil, Isopar F oil or paraffin oil) under higher temperature (150-200 ℃) melted and mixed evenly.
[0030] see figure 1 , the melt extruded through the extruder die (for extruding the melt of resin and pore-forming agent) 1 passes through longitudinal cooling rolls 2 and 3, and transverse cooling roll 4 in turn, and the melt is cooled after passing through three sets of cooling rolls Become a solid slab, coiled and wound.
[0031] see figure 2 , the cooled slab is extracted and heated and dried by one of N,N-dimethylformamide, dichloromethane and chloroform ( figure 2 ). Specifically, the slab passes through the roller 5 positioned in the trough 6 containing the extractant, passes between the heating and drying devices 11 and 12, and passes through the roller 5 positioned in the trough 10 containing...
Embodiment 1
[0043] The selected polyolefin resin is ultra-high-density polyethylene resin particles with a molecular weight of 4 million, and the pore-forming agent used is liquid paraffin oil; the weight ratio of oil powder is 15%, and the melting temperature is 150 ° C. It is melted and extruded through an extruder. The temperature of the cooling roll 2 was 70°C, the temperature of the cooling roll 3 was 63°C, and the temperature of the cooling roll 4 was 56°C. The extraction solvent in the extraction unit is N,N-dimethylformamide, the solvent is miscible with water in the feed tank 6, the volume ratio of the solvent is 80%, and the volume ratio of the solvent in the feed tank 10 is 60%. The temperature of heaters 11 and 12 is 155° C., the temperature of heaters 13 and 14 is 160° C., and the speed of extraction is 10 m / min. Carry out the first step of longitudinal stretching with a stretching ratio of 7 times, the stretching temperature is 113° C., and the stretching line speed is 20 m / ...
Embodiment 2
[0045] The selected polyolefin resin is isotactic polypropylene resin particles with a molecular weight of 200,000, and the pore-forming agent used is Isopar E oil; the weight ratio of oil to powder is 20%, and the melting temperature is 220° C., which is melted and extruded through an extruder. The temperature of the cooling roll 2 was 170°C, the temperature of the cooling roll 3 was 150°C, and the temperature of the cooling roll 4 was 130°C. The extraction solvent in the extraction unit is dichloromethane, and the solvent in feed tanks 6 and 10 is 100% solvent. The temperature of the heaters 11 and 12 is 55° C., the temperature of the heaters 13 and 14 is 60° C., and the extraction speed is 10 m / min. Carry out the first step of longitudinal stretching with a stretching ratio of 4 times, the stretching temperature is 170° C.; the stretching line speed is 15 m / min. Carry out the second step of biaxial stretching, the final stretching ratio in the transverse direction is 1:6, ...
PUM
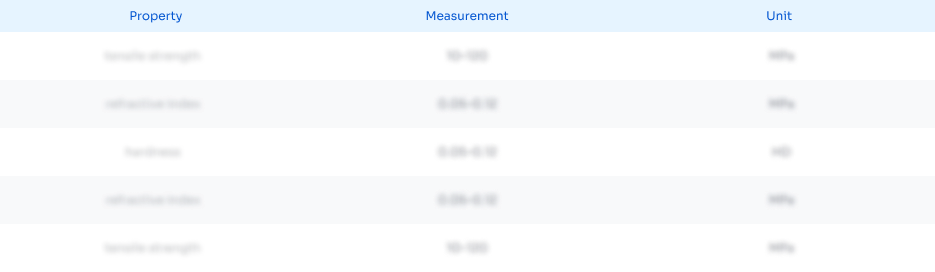
Abstract
Description
Claims
Application Information

- R&D
- Intellectual Property
- Life Sciences
- Materials
- Tech Scout
- Unparalleled Data Quality
- Higher Quality Content
- 60% Fewer Hallucinations
Browse by: Latest US Patents, China's latest patents, Technical Efficacy Thesaurus, Application Domain, Technology Topic, Popular Technical Reports.
© 2025 PatSnap. All rights reserved.Legal|Privacy policy|Modern Slavery Act Transparency Statement|Sitemap|About US| Contact US: help@patsnap.com