Full-automatic heat shrinkage tube penetrating pressing machine
A heat-shrinkable tube and crimping machine technology, which is applied to electrical components, circuits, connections, etc., can solve problems such as low production efficiency and product quality
- Summary
- Abstract
- Description
- Claims
- Application Information
AI Technical Summary
Problems solved by technology
Method used
Image
Examples
Embodiment Construction
[0075] The present invention will be described in further detail below in conjunction with the accompanying drawings and specific embodiments.
[0076] refer to Figure 1~15 , a fully automatic heat-shrinkable tube crimping machine, comprising a frame 1, a workbench 2 arranged on the frame, the workbench is provided with a tangent stripping station A, a terminal crimping station B, Wearing heat shrink tube station C and thermal bonding station D;
[0077] The wire cutting and peeling station A is provided with a wire cutting and peeling mechanism 3 for cutting and peeling the cables, and a wire feeding mechanism is provided behind the wire cutting and peeling mechanism to transport the cables forward to the wire cutting and peeling mechanism 4. A wire-drawing manipulator 5 that can pull the cable forward is provided in front of the wire-cutting and stripping mechanism;
[0078] The terminal crimping station B is provided with a terminal crimping mechanism 6 for crimping the ...
PUM
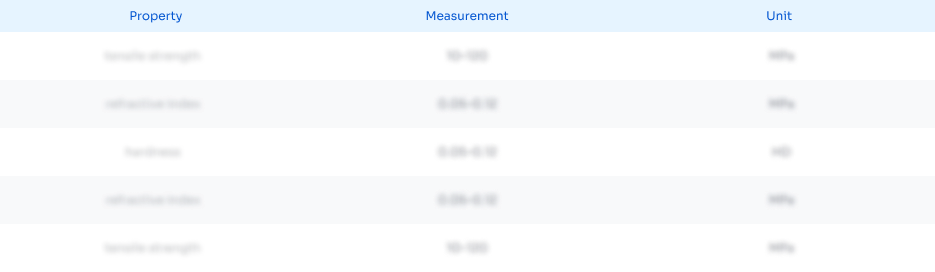
Abstract
Description
Claims
Application Information

- R&D
- Intellectual Property
- Life Sciences
- Materials
- Tech Scout
- Unparalleled Data Quality
- Higher Quality Content
- 60% Fewer Hallucinations
Browse by: Latest US Patents, China's latest patents, Technical Efficacy Thesaurus, Application Domain, Technology Topic, Popular Technical Reports.
© 2025 PatSnap. All rights reserved.Legal|Privacy policy|Modern Slavery Act Transparency Statement|Sitemap|About US| Contact US: help@patsnap.com