Surfacing welding electrode
A technology for surfacing electrodes and welding cores, applied in welding media, welding equipment, welding/cutting media/materials, etc., which can solve friction, damage to impact parts, decrease in wear and corrosion resistance of cladding, and unusable mechanical and other problems, to achieve the effect of beautiful welding seam formation, excellent welding performance and soft arc light.
- Summary
- Abstract
- Description
- Claims
- Application Information
AI Technical Summary
Problems solved by technology
Method used
Image
Examples
Embodiment 1
[0036] Cobalt 106 steel is used as the raw material to forge the welding core wire, and the chemical composition (weight percentage) of the welding core wire is:
[0037]
[0038] with TiO 2 -SiO 2 -CaO slag-based formula is coated with a drug skin, and the formula ingredients (weight percentage) are:
[0039] Slagging agent: rutile and titanium dioxide (TiO 2 ): 35%;
[0040] Mica + feldspar + bentonite (SiO 2 ): 18%;
[0041] Fluoride [CaF 2 +BaF 2 +(NaF or MgF 2 )]: 10%;
[0042] Gas generating agent: carbonate (CaCO 3 +MgCO 3 +BaCO 3 ): 20%;
[0043] Alloy agent: manganese + chromium + nickel: 17%.
[0044] In this example, the experimental hardness value is:
[0045] temperature °C
Embodiment 2
[0047] Cobalt 106 steel is used as the raw material to forge the welding core wire, and the chemical composition (weight percentage) of the welding core wire is:
[0048]
[0049] with TiO 2 -SiO 2 -CaO slag-based formula is coated with a drug skin, and the formula ingredients (weight percentage) are:
[0050] Slagging agent: rutile and titanium dioxide (TiO 2 ): 40%;
[0051] Mica + feldspar + bentonite (SiO 2 ): 15%;
[0052] Fluoride [CaF 2 +BaF 2 +(NaF or MgF 2 )]:9%;
[0053] Gas generating agent: carbonate (CaCO 3 +MgCO 3 +BaCO 3 ): 20%;
[0054] Alloy agent: manganese + chromium + nickel: 16%.
[0055] In this example, the experimental hardness value is:
[0056] temperature °C
Embodiment 3
[0058] Cobalt 106 steel is used as the raw material to forge the welding core wire, and the chemical composition (weight percentage) of the welding core wire is:
[0059]
[0060] with TiO 2 -SiO 2 -CaO slag-based formula is coated with a drug skin, and the formula ingredients (weight percentage) are:
[0061] Slagging agent: rutile and titanium dioxide (TiO 2 ): 45%;
[0062] Mica + feldspar + bentonite (SiO 2 ): 18%;
[0063] Fluoride [CaF 2 +BaF 2 +(NaF or MgF 2 )]: 7%;
[0064] Gas generating agent: carbonate (CaCO 3 +MgCO 3 +BaCO 3 ): 13%;
[0065] Alloy agent: manganese + chromium + nickel: 17%.
[0066] In this example, the experimental hardness value is:
[0067] temperature °C
PUM
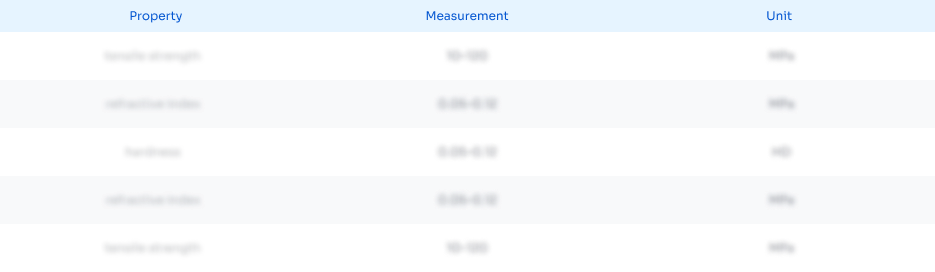
Abstract
Description
Claims
Application Information

- R&D
- Intellectual Property
- Life Sciences
- Materials
- Tech Scout
- Unparalleled Data Quality
- Higher Quality Content
- 60% Fewer Hallucinations
Browse by: Latest US Patents, China's latest patents, Technical Efficacy Thesaurus, Application Domain, Technology Topic, Popular Technical Reports.
© 2025 PatSnap. All rights reserved.Legal|Privacy policy|Modern Slavery Act Transparency Statement|Sitemap|About US| Contact US: help@patsnap.com