Production process of digital photo paper synthesized by multiple fibers
A production process and multi-fiber technology, which is applied in the production process field of multi-fiber synthetic digital photo paper, can solve the problems of high gloss, high water resistance, high ink absorption, general color reproduction, graying of printing images, etc. Thickness, Viscosity Reduction, Impact Reduction Effect
- Summary
- Abstract
- Description
- Claims
- Application Information
AI Technical Summary
Problems solved by technology
Method used
Examples
Embodiment 1
[0022] ①In-slurry sizing liquid preparation process: Add 600kg of clear water and 40kg of JF-921 cationic starch into the glue pot, stir evenly, then slowly raise the temperature to 95°C, keep it warm for 20 minutes, add water to the scale line, and stir evenly to prepare the slurry sizing solution. The glue is ready for use.
[0023] ②Preparation process of surface sizing solution: Add 400kg of clear water and 70kg of JF-922 surface sizing modified starch and YF-412 tapioca starch into the glue pot, stir well and then slowly raise the temperature to 95°C, keep it warm for 20 minutes, and add water to the mark line, and add 0.45kg of KSK468 rheology modifier, stir evenly, filter into the storage barrel, keep the temperature at 65-68°C for later use.
[0024] ③ Pulp disintegration process: bleached kraft softwood pulp with a length of 2.7mm, bleached kraft hardwood pulp with a length of 1.0mm, bamboo pulp with a length of 1.3mm, and reed pulp with a length of 1.2mm, in a weight...
Embodiment 2
[0033] ①Preparation process of the sizing solution in the pulp: same as described in Example 1.
[0034] ②Preparation process of surface sizing solution: Add 400kg of clear water and 75kg of JF-922 surface sizing modified starch and YF-412 tapioca starch into the glue pot, stir well and then slowly raise the temperature to 95°C, keep it warm for 20 minutes, add water to the scale line , and add 0.5kg of KSK468 rheology modifier, stir evenly, filter into a storage barrel, keep the temperature at 65-68°C for later use.
[0035] ③ Pulp disintegration process: bleached kraft softwood pulp with a length of 2.7 mm, bleached kraft hardwood pulp with a length of 1.0 mm, bamboo pulp with a length of 1.3 mm, and reed pulp with a length of 1.2 mm in a weight ratio of 1:6:1.5 : 1.5, 1000kg, disintegrate by hydraulic pulper, and add weight concentration 10% pigment brilliant blue 80ml, fluorescent whitening agent 1.6kg, natron 4.5kg in the disintegrated slurry, add water and dilute to weig...
PUM
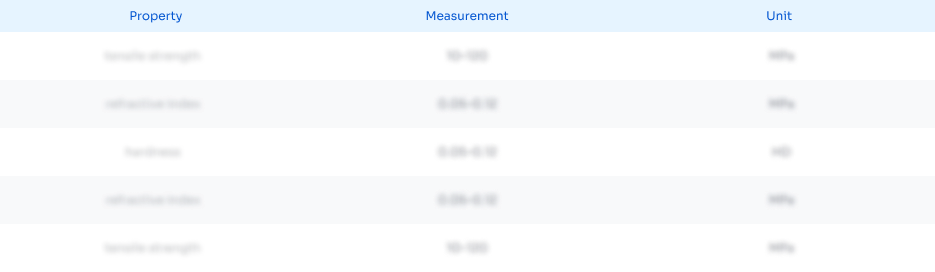
Abstract
Description
Claims
Application Information

- R&D
- Intellectual Property
- Life Sciences
- Materials
- Tech Scout
- Unparalleled Data Quality
- Higher Quality Content
- 60% Fewer Hallucinations
Browse by: Latest US Patents, China's latest patents, Technical Efficacy Thesaurus, Application Domain, Technology Topic, Popular Technical Reports.
© 2025 PatSnap. All rights reserved.Legal|Privacy policy|Modern Slavery Act Transparency Statement|Sitemap|About US| Contact US: help@patsnap.com