Preparation method of heat resistant spandex fiber
A spandex fiber, heat-resistant technology, applied in the direction of fiber chemical characteristics, textiles and papermaking, single-component synthetic polymer rayon, etc., can solve the problem of limited heat-resistant performance, unsatisfactory results, and poor viscosity of spinning solution Stability and other issues, to achieve the effect of good viscosity stability and improved heat resistance
- Summary
- Abstract
- Description
- Claims
- Application Information
AI Technical Summary
Problems solved by technology
Method used
Image
Examples
Embodiment 1
[0035] Polytetrahydrofuran PTMEG (molecular weight 1800) (82 g) and 4,4'-methylenebis(phenylisocyanate) (4,4'-MDI) (16 g) at 70 o C was reacted for 2 hours to form a prepolymer. 200 mL of DMAc solvent was added to the prepolymer to dissolve the prepolymer in the polar solvent. Add a mixture of 4,4'-diaminodiphenyl ether and ethylenediamine chain extender (10 / 90 molar ratio, 1.55 g / 0.9 g) to the prepolymer to make it react with unreacted isocyanic acid Phenyl ester and then at a temperature of 20 o C further reacted for 120 minutes until the viscosity was stable, and polymerized into polyurethane urea, the apparent viscosity at room temperature was 3200 poise. The molecular weight of the product was tested by gel permeation chromatography (GPC method), and the results are shown in Table 1.
Embodiment 2
[0037] The preparation method is the same as in Example 2, except that a mixture chain extender (15 / 85 molar ratio) of 4,4'-diaminodiphenylmethane and ethylenediamine is used. The resulting product had an apparent viscosity of 3850 poise at room temperature. The molecular weight of the product was tested by GPC, and the results are shown in Table 1.
Embodiment 3
[0039] The preparation method is the same as in Example 1, the difference is that polytetrahydrofuran (PTMEG) molecular weight 2000 is used during the prepolymerization reaction, and only p-phenylenediamine chain extender (3.4 grams) is added to the prepolymer after the prepolymerization ends, at a temperature of 70 o C react for 2 hours until the viscosity is stable. The resulting product was tested for molecular weight by GPC, and the results are shown in Table 1.
[0040] Comparative example - manufacture of conventional spandex:
[0041] The preparation method was the same as in Example 1, except that the diamine chain extender added to the prepolymer was only ethylenediamine (1.65 g), to obtain conventional spandex. Its apparent viscosity at room temperature is 4000 poise. The molecular weight was tested by GPC, and the results are shown in Table 1.
[0042] product inspection:
[0043] The molecular weight of the product prepared in the above examples was measured by...
PUM
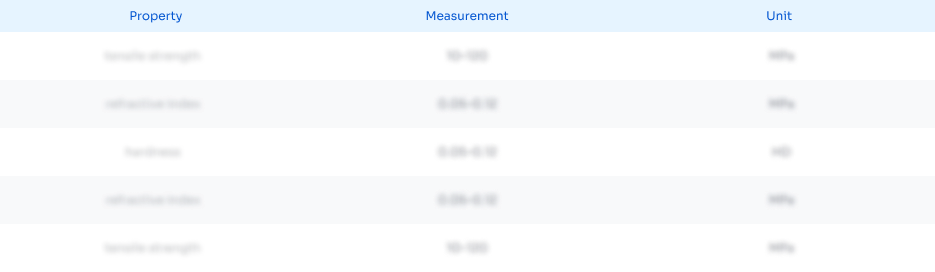
Abstract
Description
Claims
Application Information

- R&D
- Intellectual Property
- Life Sciences
- Materials
- Tech Scout
- Unparalleled Data Quality
- Higher Quality Content
- 60% Fewer Hallucinations
Browse by: Latest US Patents, China's latest patents, Technical Efficacy Thesaurus, Application Domain, Technology Topic, Popular Technical Reports.
© 2025 PatSnap. All rights reserved.Legal|Privacy policy|Modern Slavery Act Transparency Statement|Sitemap|About US| Contact US: help@patsnap.com