Semiconductor wafer electrode structure and manufacturing method thereof
A technology of wafer electrodes and manufacturing methods, applied in semiconductor/solid-state device manufacturing, semiconductor devices, semiconductor/solid-state device components, etc., can solve problems such as abnormality, asymmetric transmission, damage to the material of the light-emitting layer, electrical instability, etc. , to achieve the effect of improving the quality
- Summary
- Abstract
- Description
- Claims
- Application Information
AI Technical Summary
Problems solved by technology
Method used
Image
Examples
Embodiment Construction
[0022] First, see figure 2 As shown, the surface of the electrode 21a of the existing semiconductor wafer 20 is a planar design; see also image 3 As shown, on the semiconductor wafer 20 of the same surface layer (such as the light-emitting layer of a light-emitting diode), an electrode 21b with a rough surface is made, and observing the wire-bonding process of the two forming the ball end 11, it can be known that the electrode 21b with a rough surface is larger than the electrode with a flat surface. 21a is more resistant to (offset) ultrasonic vibrations, which can be explained as the horizontal transmission of energy is hindered by the rough surface, and the vibration energy of ultrasonic waves is difficult to transmit downwards from both sides of the rough surface electrode 21b, so the bonding process causes the wafer to produce The possibility of chipping damage is less likely to occur under the rough surface electrode 21b, but the opposite is true for the flat surface e...
PUM
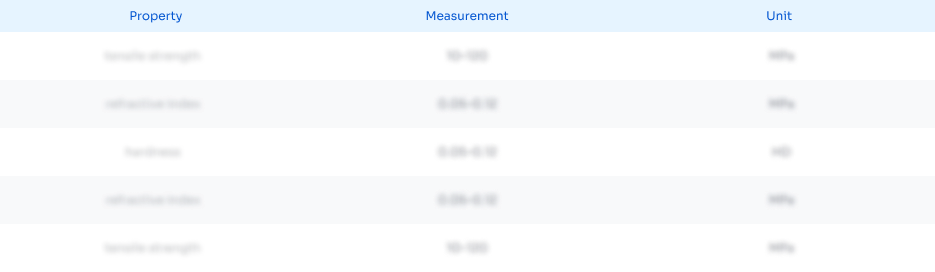
Abstract
Description
Claims
Application Information

- R&D Engineer
- R&D Manager
- IP Professional
- Industry Leading Data Capabilities
- Powerful AI technology
- Patent DNA Extraction
Browse by: Latest US Patents, China's latest patents, Technical Efficacy Thesaurus, Application Domain, Technology Topic, Popular Technical Reports.
© 2024 PatSnap. All rights reserved.Legal|Privacy policy|Modern Slavery Act Transparency Statement|Sitemap|About US| Contact US: help@patsnap.com