Ultrasonic wave wire soldering method and wire soldering apparatus
A welding wire device, ultrasonic technology, applied in welding equipment, non-electric welding equipment, electrical components, etc., can solve the problems of wasting time, welding wire speed limitation, unable to monitor and improve welding wire quality in real time, etc., to improve the welding wire speed. , Improve the quality of the welding wire, monitor the effect of the quality of the welding wire in real time
- Summary
- Abstract
- Description
- Claims
- Application Information
AI Technical Summary
Problems solved by technology
Method used
Image
Examples
Embodiment Construction
[0050] A rotary automatic ultrasonic wire welding machine such as figure 1 , 2 , 3, including a welding head system 2 with a transducer, a wire clip, a welding tip, a welding arm and wire feeding and pulling parts, and an image optical system 1 for positioning an adjustable optical lens group and a camera, A worktable 6 that can move in the horizontal direction, a turntable 5 that can rotate in the horizontal direction on the worktable 6 , and a clamp 4 that is arranged on the turntable 5 and is used to fix the workpiece 3 to be welded. The welding head system 2 is located above the center of the workbench 6 and can move vertically or horizontally. The image optical system 1 is also an image optical system for detection and is also located above the center of the workbench 6. Move in the vertical direction.
[0051] The welding head system 2 uses position signals fed back by independent vertical and horizontal positioning sensors, and the micro-controller servo board gives a...
PUM
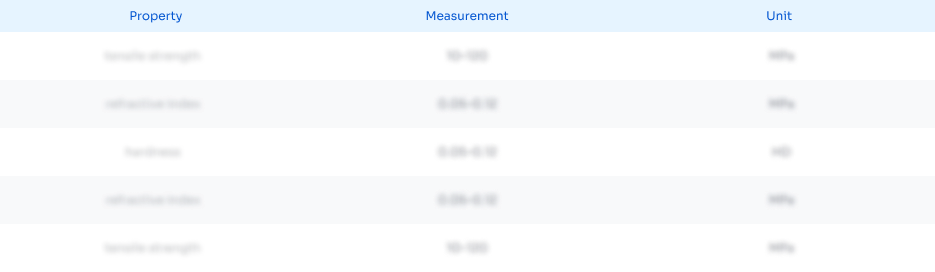
Abstract
Description
Claims
Application Information

- R&D
- Intellectual Property
- Life Sciences
- Materials
- Tech Scout
- Unparalleled Data Quality
- Higher Quality Content
- 60% Fewer Hallucinations
Browse by: Latest US Patents, China's latest patents, Technical Efficacy Thesaurus, Application Domain, Technology Topic, Popular Technical Reports.
© 2025 PatSnap. All rights reserved.Legal|Privacy policy|Modern Slavery Act Transparency Statement|Sitemap|About US| Contact US: help@patsnap.com