Method for manufacturing high-density and low-cost zinc oxide aluminum sputtering target
A zinc-aluminum oxide and manufacturing method technology, applied in the direction of sputtering plating, metal material coating process, ion implantation plating, etc., can solve the problem that it is difficult to obtain high density and high uniformity without loss of oxygen, expensive production cost, and equipment Large investment and other issues, to achieve the effect of density and uniformity of microstructure, high production efficiency and excellent quality
- Summary
- Abstract
- Description
- Claims
- Application Information
AI Technical Summary
Problems solved by technology
Method used
Examples
Embodiment Construction
[0033] In this embodiment, 1960 grams of zinc oxide powder and 40 grams of aluminum oxide powder are weighed with an electronic scale. The raw material composition is 98wt% zinc oxide+2wt% aluminum oxide, with an average particle diameter of 20 nanometers to 200 microns, and the powder purity is All greater than 99.95%. Made into mixed raw material powder.
[0034] Fully dissolve pure water, methacrylamide monomer, and N-N'dimethylbisacrylamide in a weight ratio of 100:(16-18):(0.6-1) to form a premix solution, and add 0.1-5 parts by weight Tetramethylammonium hydroxide is used as a dispersant, adding raw material powder, and ball milling to make slurry with a ball mill. The solid phase content of the raw material powder in the slurry is 50%, and the pH value of the slurry is adjusted to 9.5 by adding analytically pure ammonia water. Use zirconia balls as media in a ball mill for 15 hours, then add 0.1-1% volume of n-octanol organic degassing agent, and 0.01-0.5wt‰ ammonium p...
PUM
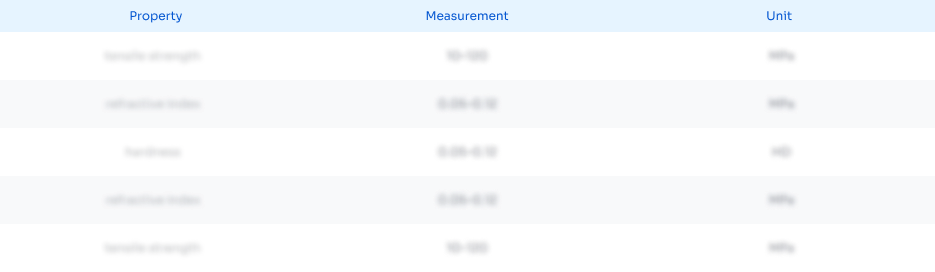
Abstract
Description
Claims
Application Information

- R&D
- Intellectual Property
- Life Sciences
- Materials
- Tech Scout
- Unparalleled Data Quality
- Higher Quality Content
- 60% Fewer Hallucinations
Browse by: Latest US Patents, China's latest patents, Technical Efficacy Thesaurus, Application Domain, Technology Topic, Popular Technical Reports.
© 2025 PatSnap. All rights reserved.Legal|Privacy policy|Modern Slavery Act Transparency Statement|Sitemap|About US| Contact US: help@patsnap.com