Manufacture process of changeable geometrical cross-section turbocharger nozzle blade
A technology of turbocharger and preparation process, used in turbines, mechanical equipment, machines/engines, etc., can solve the problems of poor melt feeding ability, low product accuracy, poor performance, etc., and achieve uniform feeding. Effect
- Summary
- Abstract
- Description
- Claims
- Application Information
AI Technical Summary
Problems solved by technology
Method used
Image
Examples
Embodiment 1
[0034] The preparation process of the nozzle ring vane of the variable geometry cross-section turbocharger is as follows:
[0035] Raw material preparation: The powder raw material used in the present invention is HK30 aerosolized powder provided by Osprey Company of the United Kingdom. The chemical composition of the powder is shown in Table 1. figure 1 It is the SEM image of the raw material powder, and its particle size distribution is as follows: figure 2 shown. In order to improve product performance, 1.5% of high-carbon affinity element Ti is added by weight percentage, and its morphology is as follows image 3 shown.
[0036] Table 1 Chemical composition of HK30 powder
[0037]
[0038] Preparation of binding agent: by weight percentage, get polyethylene glycol 10%, vegetable oil 30%, polyethylene 10%, polypropylene 5%, paraffin 45%, put in blade mixer, mix at 140 ℃ temperature 1 hour.
[0039] Preparation of feed: According to the mass ratio of 95:5%, weigh t...
Embodiment 2
[0046] The preparation process of the nozzle ring vane of the variable geometry cross-section turbocharger is as follows:
[0047] Raw material preparation: The powder raw material used in the present invention is HK30 aerosolized powder provided by Osprey Company of the United Kingdom. The chemical composition of the powder is shown in Table 1. In order to improve product performance, 1.0% of high-carbon affinity element Ti is added by weight percentage;
[0048] Preparation of binding agent: by weight percentage, get polyethylene glycol 15%, vegetable oil 30%, polyethylene 10%, polypropylene 20%, paraffin 25%, put in blade mixer, mix at 150 ℃ temperature 1.5 hours.
[0049] Preparation of feed: According to the mass ratio of 85:15%, weigh the binder and mix with HK30 and Ti powder. The mixing temperature is 130°C, the speed of the mixer is 70r / min, and the mixing time is 2.0 h. The uniformity of feeding is judged by capillary rheometer and scanning electron microscope. ...
Embodiment 3
[0054] The preparation process of the nozzle ring vane of the variable geometry cross-section turbocharger is as follows:
[0055] Raw material preparation: The powder raw material used in the present invention is HK30 aerosolized powder provided by Osprey Company of the United Kingdom. The chemical composition of the powder is shown in Table 1. In order to improve product performance, 0.5% of high-carbon affinity element Ti is added by weight percentage;
[0056] Preparation of binding agent: by weight percentage, get polyethylene glycol 15%, vegetable oil 15%, polyethylene 15%, polypropylene 20%, paraffin 35%, put in blade mixer, mix at 155 ℃ temperature 1.5 hours.
[0057] Preparation of feed: According to the mass ratio of 90:10%, weigh the binder and mix with HK30 and Ti powder. The mixing temperature is 170°C, the speed of the mixer is 50r / min, and the mixing time is 1.0 h. The uniformity of the feed is judged by the capillary rheometer and the scanning electron micr...
PUM
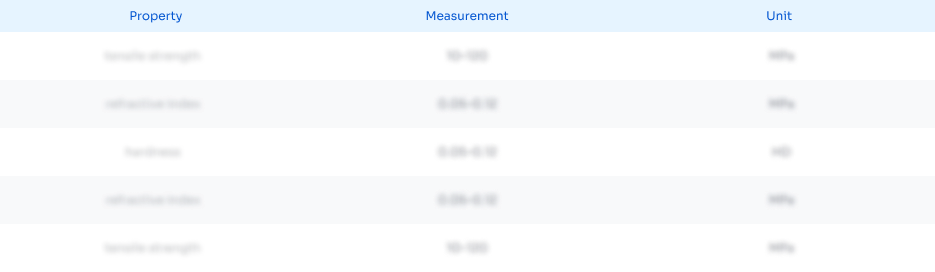
Abstract
Description
Claims
Application Information

- R&D Engineer
- R&D Manager
- IP Professional
- Industry Leading Data Capabilities
- Powerful AI technology
- Patent DNA Extraction
Browse by: Latest US Patents, China's latest patents, Technical Efficacy Thesaurus, Application Domain, Technology Topic, Popular Technical Reports.
© 2024 PatSnap. All rights reserved.Legal|Privacy policy|Modern Slavery Act Transparency Statement|Sitemap|About US| Contact US: help@patsnap.com