Method for quickly preparing metal ceramic coating through laser induced composite fusioncast
A metal-ceramic coating and laser induction technology, which is applied in metal material coating process, coating, air transportation, etc., can solve the problems of easy cracking of metal-ceramic coating, small ceramic phase injection depth, and low volume percentage , to achieve excellent wear resistance, high volume percentage, and low burning loss
- Summary
- Abstract
- Description
- Claims
- Application Information
AI Technical Summary
Problems solved by technology
Method used
Image
Examples
example 1
[0039] Using the method of laser induction compound fusion injection, cast WC particles are directly injected into the surface of nickel superalloy GH4133 to form WC / Ni cermet coating. The volume percentage of WC particles in the cermet coating is 30%, the injection depth of WC particles is 0.8mm, and the area of the coating is 100×150mm 2 .
[0040] The implementation process of this embodiment is:
[0041] (1) Selection of ceramic phase particles and preparation of substrate. Ceramic phase 8 is cast WC particles, composed of flaky WC+W 2 C has a crystal composition and an average particle size of 40 μm. It is placed in an incubator at 150° C. to dry for 2 hours, and then put into the loading hopper 7 of the automatic powder feeder 9 . The base material 14 is a nickel-based superalloy GH4133, and its chemical composition is (mass percentage) 0.032-0.038%C, 19-22%Cr, 0.05-0.07Si, 0.01-0.03Mn, 0.8-1.2%Al, 2.5-3% Ti, 1.2 ~ 1.4Nb, 0.002 ~ 0.003B, 0.01 ~ 0.02Fe, the balance ...
example 2
[0048] Using the method of laser induction composite melting injection, the MoSi 2 Particles are directly injected into the surface of TC4 alloy to form MoSi 2 / Ti cermet coating. The MoSi within the cermet coating 2 The volume percentage of particles is 50%, MoSi 2 The injection depth of the particles is 1.2mm, and the coating area is 120×180mm 2 .
[0049] The implementation process of this embodiment is:
[0050] (1) Selection of ceramic phase particles and preparation of substrate. Ceramic phase 8 is MoSi 2 The particles, whose average particle size is 50 μm, were placed in an incubator at 150° C. to dry for 2 hours, and then put into the hopper 7 of the automatic powder feeder 9 . The base material 14 is a TC4 alloy, its chemical composition is (mass percentage) 5.5-6.0% Al, 3.5-4.5% V, and the balance is Ti, and its surface is ready for use after derusting, degreasing, cleaning and sandblasting;
[0051] (2) The distance between the surface of the base material T...
example 3
[0057] Al 2 o 3 Particles are directly injected into the surface of cast aluminum alloy (Al-7wt.%Si) 2 o 3 / Al-Si cermet coating. Al in the cermet coating 2 o 3 The volume percentage of particles is 70%, Al 2 o 3The injection concentration depth of the particles is 2mm, and the coating area is 150×200mm 2 .
[0058] The implementation process of this embodiment is:
[0059] (1) Selection of ceramic phase particles and preparation of substrate. Ceramic phase 8 is Al 2 o 3 The particles, whose average particle size is 60 μm, were placed in an incubator at 150° C. to dry for 2 hours, and then put into the loading hopper 7 of the automatic powder feeder 9 . The base material 14 is cast aluminum alloy (Al-7wt.% Si), and its surface is ready for use after derusting, degreasing, cleaning and sandblasting;
[0060] (2) Adjust the distance between the surface of the base material casting aluminum alloy (Al-7wt.% Si) 14 and the induction heating coil 10 to 8mm, feed the cu...
PUM
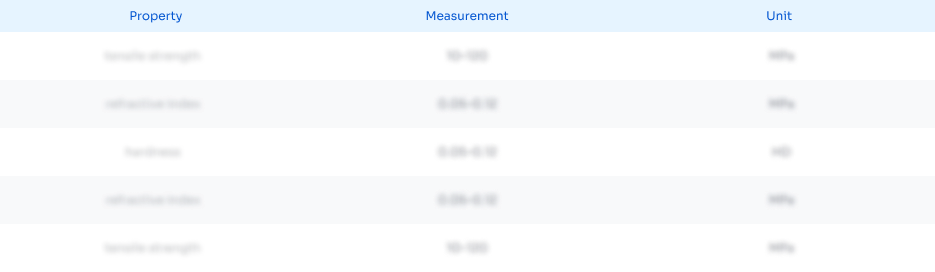
Abstract
Description
Claims
Application Information

- R&D Engineer
- R&D Manager
- IP Professional
- Industry Leading Data Capabilities
- Powerful AI technology
- Patent DNA Extraction
Browse by: Latest US Patents, China's latest patents, Technical Efficacy Thesaurus, Application Domain, Technology Topic, Popular Technical Reports.
© 2024 PatSnap. All rights reserved.Legal|Privacy policy|Modern Slavery Act Transparency Statement|Sitemap|About US| Contact US: help@patsnap.com