Steel for marine riser flange of marine deepwater drilling and manufacturing method of marine riser flange
A technology for deepwater drilling and manufacturing methods, applied in drill pipes, drilling equipment, drill pipes, etc., can solve the problems of insufficient low carbon, high strength and toughness, mechanical properties and weldability that cannot meet actual needs, etc., and achieves good strength and toughness. Forgeability, effect of good low temperature fracture toughness
- Summary
- Abstract
- Description
- Claims
- Application Information
AI Technical Summary
Problems solved by technology
Method used
Image
Examples
Embodiment 1
[0039] Test small steel ingot number: 09001
[0040] Step 1, electric arc furnace smelting, first according to the following components and content ingredients, the reference unit of each component is Wt%: C0.17, Mn1.72, Mo0.3, Nb0.054, V0.05, Ti0.015, Ni0.6, Cu0.14, Cr0.06, Si0.16, S0.005, P0.01, the balance is Fe; then conduct electric arc furnace smelting to obtain molten steel, and remove harmful substances in the steel as much as possible during smelting Elemental and non-metallic inclusions;
[0041] Step 2. Vacuum refining. The molten steel obtained in step 1 is heated by electric arc and blown with argon gas to stir the molten steel under vacuum for degassing. The technical requirements for controlling the gas content of the steel are: [H]≤2ppm, [ O】≤20ppm, 【N】≤100ppm; 【S】≤0.010%;
[0042] Step 3. Steel ingot pouring. The inert gas is blown into the molten steel by using a blow-up sliding nozzle to uniform the composition and temperature, and purify the molten steel. T...
Embodiment 2
[0047] Test furnace number: 09303161444
[0048] Step 1, electric arc furnace smelting, first according to the following components and content ingredients, the reference unit of each component is Wt%: C0.18, Mn1.79, Mo0.29, Nb0.058, V0.079, Ti0.002, Ni0.89, Cu0.14, Cr0.14, Si0.2, S0.004, P0.019, the balance is Fe; then smelting in an electric arc furnace to obtain molten steel, and remove harmful substances in the steel as much as possible during smelting Elemental and non-metallic inclusions;
[0049] Step 2. Vacuum refining. The molten steel obtained in step 1 is heated by electric arc and blown with argon gas to stir the molten steel under vacuum for degassing. The technical requirements for controlling the gas content of the steel are: [H]≤2ppm, [ O】≤20ppm, 【N】≤100ppm; 【S】≤0.010%;
[0050] Step 3. Steel ingot pouring. The inert gas is blown into the molten steel by using a blow-up sliding nozzle to uniform the composition and temperature, and purify the molten steel. Th...
Embodiment 3
[0055] Test furnace number: 09303081817
[0056] Step 1, electric arc furnace smelting, first according to the following components and content ingredients, the reference unit of each component is Wt%: C0.18, Mn1.8, Mo0.29, Nb0.058, V0.08, Ti0.002, Ni0.9, Cu0.15, Cr0.15, Si0.2, S0.004, P0.019, the balance is Fe; then conduct electric arc furnace smelting to obtain molten steel, and remove harmful substances in the steel as much as possible during smelting Elemental and non-metallic inclusions;
[0057] Step 2. Vacuum refining. The molten steel obtained in step 1 is heated by electric arc and blown with argon gas to stir the molten steel under vacuum for degassing. The technical requirements for controlling the gas content of the steel are: [H]≤2ppm, [ O】≤20ppm, 【N】≤100ppm; 【S】≤0.010%;
[0058] Step 3. Steel ingot pouring. The inert gas is blown into the molten steel by using a blow-up sliding nozzle to uniform the composition and temperature, and purify the molten steel. The...
PUM
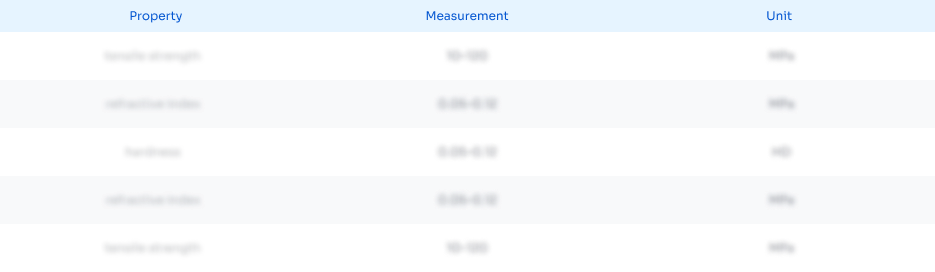
Abstract
Description
Claims
Application Information

- R&D
- Intellectual Property
- Life Sciences
- Materials
- Tech Scout
- Unparalleled Data Quality
- Higher Quality Content
- 60% Fewer Hallucinations
Browse by: Latest US Patents, China's latest patents, Technical Efficacy Thesaurus, Application Domain, Technology Topic, Popular Technical Reports.
© 2025 PatSnap. All rights reserved.Legal|Privacy policy|Modern Slavery Act Transparency Statement|Sitemap|About US| Contact US: help@patsnap.com