Process for the alkylation of benzene with isopropanol or blends of isopropanol and propylene
An isopropanol and alkylation technology, applied in the field of alkylation, can solve the problems of environmental impact safety, complex catalyst use, etc., and achieve the effect of high productivity
- Summary
- Abstract
- Description
- Claims
- Application Information
AI Technical Summary
Problems solved by technology
Method used
Image
Examples
Embodiment 1
[0074] Alkylation experiments with benzene were carried out with isopropanol using the experimental setup described below.
[0075]The test rig consisted of the following: tanks for the benzene and isopropanol reactants, feed pumps for feeding the reactants into the reactor, preheating means for the reactants, a steel reactor located in an electric furnace, temperature regulation inside the reactor loops, pressure regulation loops within the reactor, coolant for the reactor effluent, and collection systems for liquid and gaseous products.
[0076] In particular, the reactor consists of a cylindrical steel tube with a mechanical sealing system and a diameter equal to about 2 cm.
[0077] Along the larger axis of the reactor there is a thermometric cavity with a diameter equal to 1 mm, inside which is contained a thermocouple freely sliding along the larger axis of the reactor.
[0078] A catalyst comprising ZSM-12 zeolite prepared as described in Example 2 of WO 2003 / 0069459 w...
Embodiment 2
[0095] Embodiment 2 (comparison)
[0096] The results obtained in the preceding examples were compared with those obtained using a catalyst comprising zeolite beta prepared as described in Example 4 of EP 847802 .
[0097] Both catalysts of Example 1 and Comparative Example 2 contained about 50% active phase.
[0098] Using the same experimental setup as described in Example 1, operating under the same operating conditions, it was ensured that the reactants were in the gas phase and the product part was in the liquid phase.
[0099] Assignment of the physical state of the reactant mixture was performed as previously described in Example 1.
[0100] figure 2 The trends in molar selectivity [Ar] / [IPA] and molar selectivity [Cum] / [IPA] compared to catalyst productivity are depicted.
[0101] After about 160 hours of operation, the alcohol conversion had decreased by 2.5%. This value clearly indicates the greater stability and thus its higher productivity when using the catal...
PUM
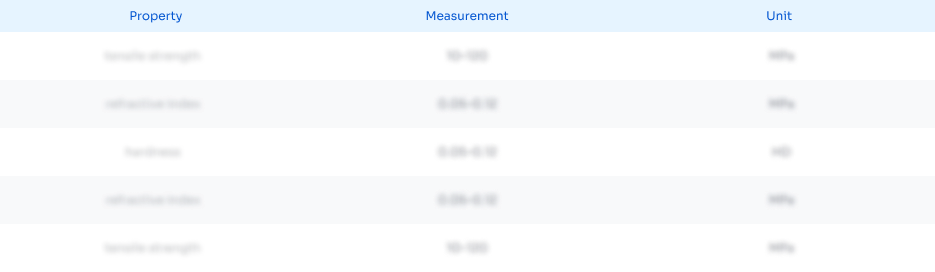
Abstract
Description
Claims
Application Information

- R&D
- Intellectual Property
- Life Sciences
- Materials
- Tech Scout
- Unparalleled Data Quality
- Higher Quality Content
- 60% Fewer Hallucinations
Browse by: Latest US Patents, China's latest patents, Technical Efficacy Thesaurus, Application Domain, Technology Topic, Popular Technical Reports.
© 2025 PatSnap. All rights reserved.Legal|Privacy policy|Modern Slavery Act Transparency Statement|Sitemap|About US| Contact US: help@patsnap.com