Method and apparatus for recovery of molybdenum from spent catalysts
A waste catalyst and equipment technology, applied in the field of molybdenum recovery, can solve the problems of maximum volume fraction limitation, affecting operation efficiency and strength, etc.
- Summary
- Abstract
- Description
- Claims
- Application Information
AI Technical Summary
Problems solved by technology
Method used
Image
Examples
Embodiment
[0051] Multiple pilot-scale experiments were performed with various molybdenum-containing feedstocks to demonstrate method performance. The pilot test was carried out with the following system configurations and devices: ball mill pulverization system, loss-in-weight screw feeder for conveying the raw material, combustion air delivery system, oxygen delivery system, reverse rotation vortex reactor and Entrained flow reactor assembly consisting of cyclone reactor, high temperature cyclone separator, gas quenching assembly, low temperature dust collector and acid gas scrubber. In this pilot-scale system it is provided to collect a stream similar to Product 1 (the alumina / silica rich stream exiting the high temperature cyclone, also known as by-product) and a stream somewhat similar to Product 2 (The molybdenum trioxide-rich stream exiting the cryogenic dust collector, also referred to herein as BH product). The BH product in this pilot test did not fully replicate Product 2 bec...
PUM
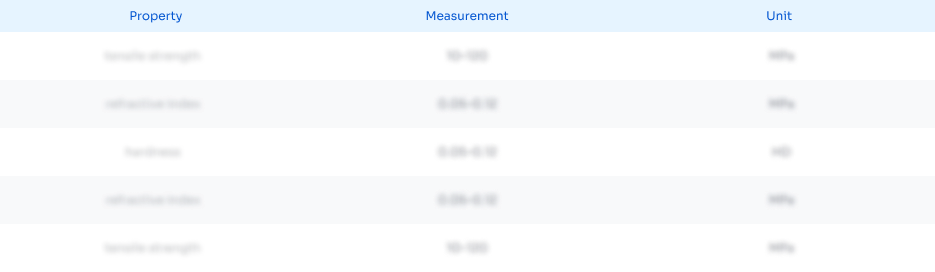
Abstract
Description
Claims
Application Information

- R&D Engineer
- R&D Manager
- IP Professional
- Industry Leading Data Capabilities
- Powerful AI technology
- Patent DNA Extraction
Browse by: Latest US Patents, China's latest patents, Technical Efficacy Thesaurus, Application Domain, Technology Topic, Popular Technical Reports.
© 2024 PatSnap. All rights reserved.Legal|Privacy policy|Modern Slavery Act Transparency Statement|Sitemap|About US| Contact US: help@patsnap.com