Pulping technology of cotton linter
A technology of cotton linter production and cotton linters, which is applied in the field of papermaking cellulose, can solve the problems of unclean removal of cottonseed husks, high price of hydrogen peroxide, and high cost of cotton pulp, achieving long insulation retention time and saving equipment investment , the effect of fast settling speed
- Summary
- Abstract
- Description
- Claims
- Application Information
AI Technical Summary
Problems solved by technology
Method used
Examples
Embodiment approach
[0026] As an embodiment of the present invention, the cotton linters pulping process includes the following steps:
[0027] A)、Linter pulping:
[0028] Using cotton linters as raw materials, under normal pressure, the temperature is below 85 ℃, adding alkali 2.5-3.5%, cooking time 25-35 minutes to prepare cotton pulp, or directly bleached without alkali soaking and cooking, and then containing Treated with chlorine 3.5-5.2% and pH 3.2-4.4 for 30-50 minutes to prepare cotton pulp;
[0029] B) Black liquor silicon evolution:
[0030] It also includes a flue gas absorption device. The flue gas absorption device is a foam tower with high mass transfer efficiency. The defoamer used is kerosene. The dilute black liquor from the pulp washing machine uses flue gas as a neutralizer. The flue gas is boiler flue gas after water film dust removal. After neutralization, silicon is evolved. The reaction principle is CO in the flue gas. 2 Lower the pH of the black liquor to 8.5-9.0. Under this pH c...
PUM
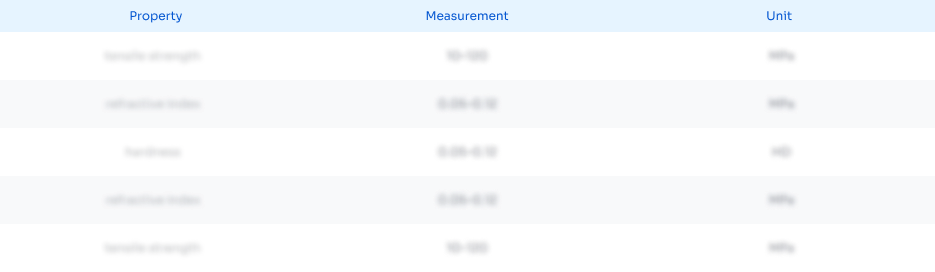
Abstract
Description
Claims
Application Information

- R&D
- Intellectual Property
- Life Sciences
- Materials
- Tech Scout
- Unparalleled Data Quality
- Higher Quality Content
- 60% Fewer Hallucinations
Browse by: Latest US Patents, China's latest patents, Technical Efficacy Thesaurus, Application Domain, Technology Topic, Popular Technical Reports.
© 2025 PatSnap. All rights reserved.Legal|Privacy policy|Modern Slavery Act Transparency Statement|Sitemap|About US| Contact US: help@patsnap.com