Alloy steel roller and manufacturing process thereof
A manufacturing process and technology of alloy steel, applied in the field of alloy steel rolls to achieve the effect of high hardness and wear resistance
- Summary
- Abstract
- Description
- Claims
- Application Information
AI Technical Summary
Problems solved by technology
Method used
Image
Examples
Embodiment 1
[0031] One of the embodiments of the present invention is an alloy steel roll, the alloy steel in the alloy steel roll contains the following components: by weight percentage, the content of carbon (C) is 0.60%, the content of silicon (Si) is 1.6% %, the content of manganese (Mn) is 1.75%, the content of chromium (Cr) is 1.6%, the content of molybdenum (Mo) is 0.25%, the content of nickel (Ni) is 0.25%, and the content of vanadium (V) is 0.08% %, the content of niobium (Nb) is 0.06%, and the content of sulfur (S) and phosphorus (P) is less than or equal to 0.025%.
[0032] The technical solution of the present invention also provides a manufacturing process for producing alloy steel rolls using the above-mentioned alloy components. The manufacturing process includes a smelting process, a forging process and a heat treatment process. It is characterized in that the process steps of the above-mentioned process are:
[0033] The first step: smelting process, the smelting process ...
Embodiment 2
[0048] One of embodiment of the present invention is a kind of alloy steel roll, and the alloy steel in this alloy steel roll contains following composition: by weight percentage, the content of carbon (C) is 0.68%, the content of silicon (Si) is 1.8% %, the content of manganese (Mn) is 1.85%, the content of chromium (Cr) is 1.8%, the content of molybdenum (Mo) is 0.35%, the content of nickel (Ni) is 0.5%, and the content of vanadium (V) is 0.10% %, the content of niobium (Nb) is 0.08%, and the content of sulfur (S) and phosphorus (P) is less than or equal to 0.025%.
[0049] The technical solution of the present invention also provides a manufacturing process for producing alloy steel rolls using the above-mentioned alloy components. The manufacturing process includes a smelting process, a forging process and a heat treatment process. It is characterized in that the process steps of the above-mentioned process are:
[0050] The first step: smelting process, the smelting proce...
Embodiment 3
[0060] One of the embodiments of the present invention is an alloy steel roll, the alloy steel in the alloy steel roll contains the following components: by weight percentage, the content of carbon (C) is 0.64%, the content of silicon (Si) is 1.7% %, the content of manganese (Mn) is 1.80%, the content of chromium (Cr) is 1.7%, the content of molybdenum (Mo) is 0.30%, the content of nickel (Ni) is 0.375%, and the content of vanadium (V) is 0.09% %, the content of niobium (Nb) is 0.07%, the content of aluminum (Al) is 0.0225%, and the content of sulfur (S) and phosphorus (P) is less than or equal to 0.025%.
[0061] The technical solution of the present invention also provides a manufacturing process for producing alloy steel rolls using the above-mentioned alloy components. The manufacturing process includes a smelting process, a forging process and a heat treatment process. It is characterized in that the process steps of the above-mentioned process are:
[0062] The first ste...
PUM
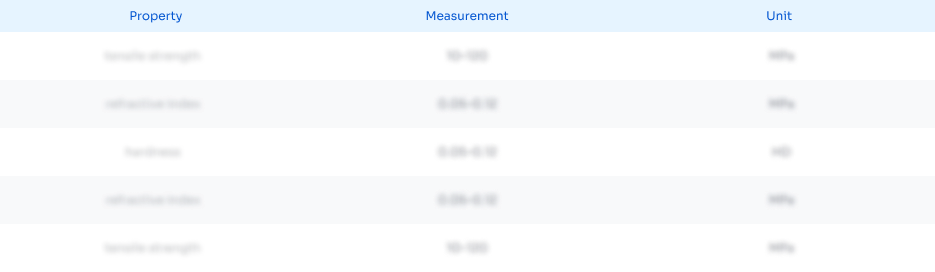
Abstract
Description
Claims
Application Information

- Generate Ideas
- Intellectual Property
- Life Sciences
- Materials
- Tech Scout
- Unparalleled Data Quality
- Higher Quality Content
- 60% Fewer Hallucinations
Browse by: Latest US Patents, China's latest patents, Technical Efficacy Thesaurus, Application Domain, Technology Topic, Popular Technical Reports.
© 2025 PatSnap. All rights reserved.Legal|Privacy policy|Modern Slavery Act Transparency Statement|Sitemap|About US| Contact US: help@patsnap.com