Catalyst for complete methanation of synthesis gas from coal and preparation method thereof
A complete methanation and coal-to-synthesis gas technology, applied in the direction of producing hydrocarbons from carbon oxides, can solve problems such as not suitable for coal-to-natural gas projects, lack of operating experience, and small number of developments, and achieve the goal of reducing cracking carbon deposits Hazard, increase catalytic activity, effect of increasing surface area
- Summary
- Abstract
- Description
- Claims
- Application Information
AI Technical Summary
Problems solved by technology
Method used
Image
Examples
Embodiment 1
[0030] The mass percent content of each component of the present embodiment is: the NiO content is 60% of the total mass of the catalyst, the Al 2 o 3 The content is 20% of the total mass of the catalyst, and the content of MgO is 8% of the total mass of the catalyst; the first auxiliary rare earth metal oxide La 2 o 3 The content is 8% of the total mass of the catalyst, the content of the second auxiliary agent basic oxide CaO is 2% of the total mass of the catalyst, and the content of graphite is 2% of the total mass of the catalyst.
[0031] The preparation method of the present embodiment comprises the following steps:
[0032] Step 1, 8.53 grams of active Al 2 o 3 Mixed with 3.41 grams of MgO, roasted in a muffle furnace at a constant temperature of 1000°C for 6 hours to form a magnesium-aluminum spinel structure, and cooled for later use;
[0033] Step 2, take by weighing 99.62 grams of hydrated nickel nitrate Ni (NO 3 ) 2 ·6H 2 O, 7.18 grams of water and lanthan...
Embodiment 2
[0040] The mass percent content of each component of the present embodiment is: the NiO content is 55% of the total mass of the catalyst, the Al 2 o 3 The content is 25% of the total mass of the catalyst, and the content of MgO is 10% of the total mass of the catalyst; the first additive is rare earth metal oxide La 2 o 3 The content is 3% of the total mass of the catalyst and Sm 2 o 3 The content is 3% of the total mass of the catalyst, the content of the second auxiliary agent basic oxide BaO is 2% of the total mass of the catalyst, and the content of graphite is 2% of the total mass of the catalyst.
[0041] The preparation method of the present embodiment comprises the following steps:
[0042] Step 1, 10.66 grams of active Al 2 o 3 Mix it with 4.27 grams of MgO, and roast it in a muffle furnace at a constant temperature of 1000°C for 6 hours to form a magnesium-aluminum spinel structure, and cool it for later use;
[0043] Step 2, take by weighing 91.31 grams of hy...
Embodiment 3
[0050] The mass percentages of each component in this embodiment are: NiO content is 44% of the total mass of the catalyst, Al 2 o 3 The content is 30% of the total mass of the catalyst, and the content of MgO is 15% of the total mass of the catalyst; the first additive is rare earth metal oxide La 2 o 3 The content is 6% of the total mass of the catalyst, the content of the second auxiliary agent basic oxide CaO is 4% of the total mass of the catalyst, and the content of graphite is 1% of the total mass of the catalyst.
[0051] The preparation method of the present embodiment comprises the following steps:
[0052] Step 1, 12.80 grams of active Al 2 o 3 Mix it with 6.40 grams of MgO, roast it in a muffle furnace at a constant temperature of 1000°C for 8 hours to form a magnesium-aluminum spinel structure, and cool it for later use;
[0053] Step 2, take by weighing 73.07 grams of hydrated nickel nitrate Ni (NO 3 ) 2 ·6H 2 O, 5.39 grams of water and lanthanum nitrate ...
PUM
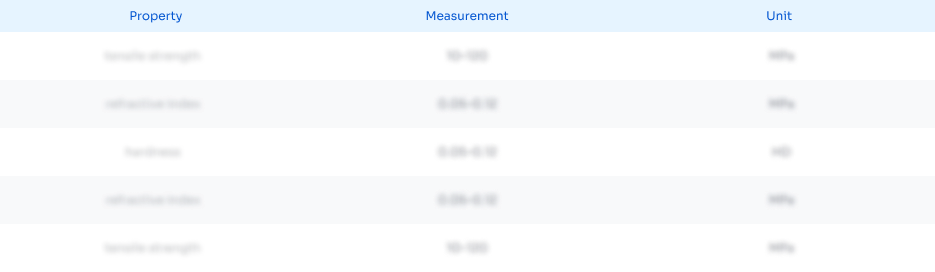
Abstract
Description
Claims
Application Information

- R&D
- Intellectual Property
- Life Sciences
- Materials
- Tech Scout
- Unparalleled Data Quality
- Higher Quality Content
- 60% Fewer Hallucinations
Browse by: Latest US Patents, China's latest patents, Technical Efficacy Thesaurus, Application Domain, Technology Topic, Popular Technical Reports.
© 2025 PatSnap. All rights reserved.Legal|Privacy policy|Modern Slavery Act Transparency Statement|Sitemap|About US| Contact US: help@patsnap.com