Fast-setting castable for main runner for COREX furnace and production technology thereof
A castable and process technology, applied in the field of quick-drying castables in the main trench of COREX furnace, can solve the problems of waste of resources, affecting production, spalling, etc., and achieve excellent results
- Summary
- Abstract
- Description
- Claims
- Application Information
AI Technical Summary
Problems solved by technology
Method used
Image
Examples
Embodiment 1
[0084] The particle size and mass percentage of each component are:
[0085] Fused dense corundum 5-8mm: 12%;
[0086] Brown corundum 3~5mm: 22%;
[0087] Tabular alumina 1~3mm: 20%;
[0088] Activated alumina powder <3um: 14%;
[0089] Silicon carbide 1~3mm: 8%;
[0090] 320 mesh silicon carbide 0.048mm: 12%;
[0091] Spherical asphalt: 5%;
[0092] Metal magnesium powder: 1%;
[0093] Sodium hexametaphosphate: 0.8%;
[0094] Lithium carbonate: 0.4%;
[0095] Polyethylene organic fiber: 2.8%;
[0096] Silicon fume: 2%.
[0097] Such a ratio is suitable for use as a castable in the manufacture of new trenches, with strong thermal shock resistance and good erosion resistance.
Embodiment 2
[0099] The particle size and mass percentage of each component are:
[0100] Fused dense corundum 5-8mm: 15%;
[0101] Brown corundum 3~5mm: 20%;
[0102] Tabular alumina 1~3mm: 20%;
[0103] Activated alumina powder <3um: 12%;
[0104] Silicon carbide 1~3mm: 9%;
[0105] 320 mesh silicon carbide 0.048mm: 11%;
[0106] Spherical asphalt: 3.3%;
[0107] Metal aluminum powder: 1%;
[0108] Sodium hexametaphosphate: 1%;
[0109] Lithium carbonate: 0.7%;
[0110] Polyethylene organic fiber: 4%;
[0111] Silicon fume: 3%.
[0112] This kind of ratio has good explosion-proof effect, more lithium carbonate, and strong quick-drying ability, so it is more suitable as a repair material. The following table is the performance index that the present invention reaches:
[0113]
[0114] It can be seen that the effect of the present invention is higher than the national requirement.
[0115] The present invention also relates to a process for producing quick-drying castables ...
PUM
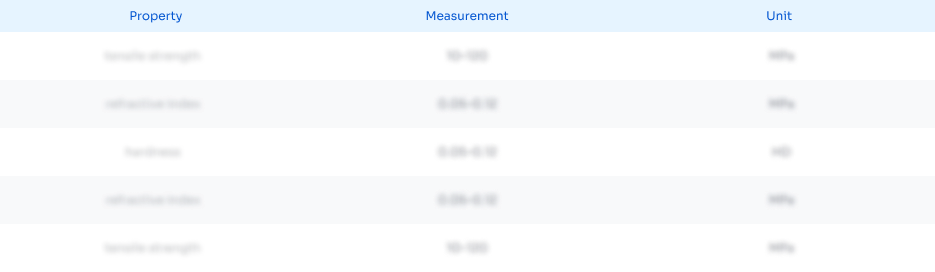
Abstract
Description
Claims
Application Information

- Generate Ideas
- Intellectual Property
- Life Sciences
- Materials
- Tech Scout
- Unparalleled Data Quality
- Higher Quality Content
- 60% Fewer Hallucinations
Browse by: Latest US Patents, China's latest patents, Technical Efficacy Thesaurus, Application Domain, Technology Topic, Popular Technical Reports.
© 2025 PatSnap. All rights reserved.Legal|Privacy policy|Modern Slavery Act Transparency Statement|Sitemap|About US| Contact US: help@patsnap.com